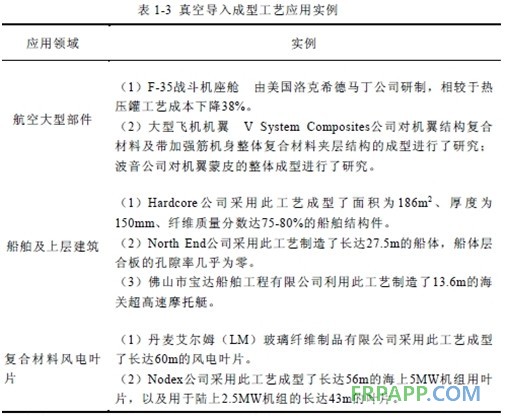
真空導(dǎo)入成型工藝的廣泛應(yīng)用和其特有的成型優(yōu)勢是分不開的。與傳統(tǒng)的開模成型工藝相比,真空導(dǎo)入成型的優(yōu)點[21,22]體現(xiàn)為:
(1)機械性能高 在相同成本下,真空導(dǎo)入成型制件的強度、剛度或硬度較之手糊成型制件可提高1.5倍以上。
(2)重復(fù)性好 通過設(shè)置真空度,可以在一定程度上控制樹脂和纖維的比例,使成型構(gòu)件具有高度一致性。
(3)成本低 樹脂浪費率低于5%,比開模工藝可節(jié)約勞動力50%以上。尤其對于大型加筋結(jié)構(gòu),材料和人工的節(jié)省相當(dāng)可觀。
(4)環(huán)保 開模成型時,苯乙烯的揮發(fā)量高達35%~45%;真空導(dǎo)入成型中,揮發(fā)性有機物和有毒物質(zhì)均被局限于真空袋中,有效的避免了對環(huán)境的污染和對人身健康的危害。
此外,與傳統(tǒng)的RTM工藝相比[23,24],真空導(dǎo)入成型只需要單面剛性模具,制品尺寸和形狀受限更少,并且不需要繁雜的注射設(shè)備,進一步降低了
成本,更適用于制造大型承力結(jié)構(gòu)。
真空導(dǎo)入成型工藝為小批量、大尺寸構(gòu)件以及加筋異型構(gòu)件的制作提供了嶄新的思路,具有非常好的前景。國外對于真空導(dǎo)入成型工藝的研究已相對成熟[25-29],國內(nèi)研究由于起步較晚,理論方面相對不完善,實踐經(jīng)驗不足。針對實際生產(chǎn)中采用試錯法進行工藝設(shè)計的窘迫局面,未來的研究方向主要集中在一下幾點:
(1)開發(fā)配套的成型設(shè)備和材料,減少對外國進口產(chǎn)品的依賴,真正實現(xiàn)獨立自主的設(shè)計開發(fā)。
(2)對樹脂在增強材料預(yù)成型體中的流動行為進行數(shù)值模擬,力求實現(xiàn)流動的可視化監(jiān)控,及時發(fā)現(xiàn)成型缺陷并進行補救,以解決真空導(dǎo)入成型構(gòu)件厚度太大時無法進行質(zhì)量檢測的痼疾。
(3)研究各種輔助介質(zhì)如導(dǎo)流布、剝離層對樹脂流動行為的影響,以更好的進行澆注系統(tǒng)的設(shè)計。
(4)對增強材料預(yù)成型技術(shù)進行研究,分析外界條件的變化對預(yù)成型體滲透率的影響,從而更好地設(shè)計鋪層順序,避免成型缺陷的產(chǎn)生。
1.2.3計算機輔助工藝設(shè)計系統(tǒng)在復(fù)合材料領(lǐng)域的應(yīng)用現(xiàn)狀在傳統(tǒng)的機械加工領(lǐng)域,計算機輔助工藝設(shè)計( CAPP)由于其有助于提高工藝設(shè)計效率、降低生產(chǎn)成本的特點已得到廣泛應(yīng)用。在復(fù)合材料領(lǐng)域,復(fù)合材料成型構(gòu)件正趨于多樣化,對其工藝設(shè)計要求越來越高,因此訃算機輔助工藝設(shè)計系統(tǒng)水到渠成的應(yīng)用于復(fù)合材料制件的工藝設(shè)計中。國外針對復(fù)合材料計算機輔助工藝設(shè)計的研究始于上世紀(jì)90年代,國內(nèi)在研究時間上相對較晚。目前國內(nèi)外的復(fù)合材料CAPP系統(tǒng)主要有[30-32]
1996年,美國設(shè)計工程學(xué)院發(fā)布了旨在提高復(fù)合材料注射工藝制造效率的ACES系統(tǒng)。該系統(tǒng)成功集成了外部計算機輔助設(shè)計軟件以及數(shù)據(jù)管理分析工具等,并通過加入RTM工藝相關(guān)知識充實了其知識庫。
Dow-UT復(fù)合材料公司開發(fā)的AdvRTM系統(tǒng)是針對RTM工藝的CAPP系統(tǒng)。該系統(tǒng)包括工藝工序排序和成本估算量兩個模型。通過將基于規(guī)則的推理與基于模型的推理兩種方法相結(jié)合,對RTM的工藝工序進行模擬,并在此基礎(chǔ)上進行成本的估算最終達到優(yōu)化的目的。
為了設(shè)計制作陶瓷基與金屬基復(fù)合材料多孔預(yù)成型體,Delaware大學(xué)與Lanxide公司聯(lián)合開發(fā)了DSSPreform系統(tǒng)。利用基于知識推理與基于模型推理方法,DSSPreform系統(tǒng)通過材料子系統(tǒng)確定成型材料,通過工藝選擇子系統(tǒng)選擇成型工藝,最后通過工藝設(shè)計子系統(tǒng)完成工藝參數(shù)設(shè)置。
California大學(xué)完成了基于注射制造系統(tǒng)的S-APD系統(tǒng)的原型系統(tǒng),采用基于知識推理和模型推理的方法來完成復(fù)合材料生產(chǎn)設(shè)備的選擇、注射過程工藝參數(shù)的優(yōu)化以及制件粘接過程模型化等工作。
通過對樹脂基復(fù)合材料成型工藝知識的集成,Michigan大學(xué)開發(fā)的Socharis系統(tǒng)對手糊成型工藝等復(fù)合材料制件成型工藝進行比較選擇以及參數(shù)設(shè)計。系統(tǒng)采用遺傳算法完成模型的推理過程,具有描述工藝的詳細步驟、確定工藝參數(shù)等功能,主要解決成型工藝的排序與選擇任務(wù)。
北京航空航天大學(xué)開發(fā)的復(fù)合材料構(gòu)件計算機輔助成型工藝系統(tǒng)利用基于特征的工藝推理方法對復(fù)合材料成型進行相似檢索,解決了復(fù)合材料成型工藝參數(shù)種類多、管理困難、設(shè)計經(jīng)驗無法共享等問題,建立了材料庫、模具庫、事例庫等系統(tǒng)支撐環(huán)境庫。
綜上所述,計算機輔助工藝設(shè)計在提高復(fù)合材料成型工藝設(shè)計效率方面具有非常重要的作用。從世界范圍來看,目前的研究正處于理論階段,很少應(yīng)用到工程實際中。隨著復(fù)合材料成型的進一步發(fā)展,相信在不遠的將來,計算機輔助工藝設(shè)計將在復(fù)合材料制件生產(chǎn)中發(fā)揮巨大作用。
1.3本課題主要研究內(nèi)容
本課題的研究內(nèi)容主要有以下幾個方面:
(1)游艇艇體真空導(dǎo)入成型工藝模型分析
通過對游艇艇體真空導(dǎo)入成型工藝過程的分析,建立艇體真空導(dǎo)入成型 充模過程的數(shù)學(xué)模型,并結(jié)合生產(chǎn)中的實踐經(jīng)驗,展開系統(tǒng)的理論研究,進一步完善工藝設(shè)計的細節(jié)。分析影響艇體成型的關(guān)鍵因素及其成型缺陷,明確各個工藝參數(shù)的設(shè)置要求以及成型材料材選擇原則。
(2)面向艇體的真空導(dǎo)入成型工藝設(shè)計系統(tǒng)框架研究
基于對游艇艇體真空導(dǎo)入成型的理論研究,將CAD/CAPP/CAM/CAE技術(shù)集成,構(gòu)建面向艇體的真空導(dǎo)入成型工藝設(shè)計系統(tǒng)的功能框架,以實現(xiàn)自動化工藝設(shè)計、工藝模擬及管理。
(3)艇體澆注系統(tǒng)仿真分析
分析樹脂在模腔內(nèi)的流動本質(zhì),建立艇體三維模型。利用PAM-RTM對充模過程進行仿真,選擇合理的流道布置方式。在最佳流道布置基礎(chǔ)上,進一步對澆口位置進行仿真,以充模時間最短為目標(biāo),結(jié)合成本最小化這一原則,利用插值擬合方法得出最佳澆口位置。
(4)艇體鋪層方案可制造性分析
分析常用增強材料性能,并建立艇體真空導(dǎo)入成型中的滲透率模!析其求解過程。利用PAM-RTM對不同鋪層方案下的艇體進行充模仿真,最終成型無缺陷為目標(biāo)對其可制造性進行評價,得出合理的鋪層方案 。
(5)面向艇體的真空導(dǎo)入成型工藝設(shè)計系統(tǒng)開發(fā)
構(gòu)建系統(tǒng)的軟件結(jié)構(gòu),在Visual C++平臺上進行原型系統(tǒng)開發(fā)。三括系統(tǒng)各文件存儲路徑的規(guī)劃、工藝參數(shù)的設(shè)計、工藝過程的數(shù)值模擬實現(xiàn)系 與系統(tǒng)Pro/E、HyperMesh、PAM-RTM等軟件的集成。