在實際應用中,SMC/BMC制品往往是作為一個部件使用,因此,存在著與其它材料部件的配合、連接及加工的問題。SMC/BMC制品具有其它材料不具備的優(yōu)點,可以成型非常復雜的形狀,但是,要成型出全部細節(jié)是不可能的。因此,必須用到SMC/BMC制品的機械加工性能、連接性能等工藝性能。一般來說,SMC/BMC制品質(zhì)脆、層間強度低、抗沖擊性能差。在進行材料加工時,一定要考慮這些特點。
1.機械加工
(1)切割加工
SMC制品的切割加工方法有手工切割、機械切割、高壓水切割。
(a)手工切割
SMC制品的手工加工作業(yè)是非常多的。常用的使用工具有刮刀、銼刀、鋼鋸、刻刀、紗帶拋光機、砂輪打磨機、金剛石研磨盤、鉆頭等。根據(jù)加工部分是平面還是曲面,是切斷還是切削等不同情況分別使用。常用的手動切割工具如圖所示。常見的手工切割工作內(nèi)容如圖所示。
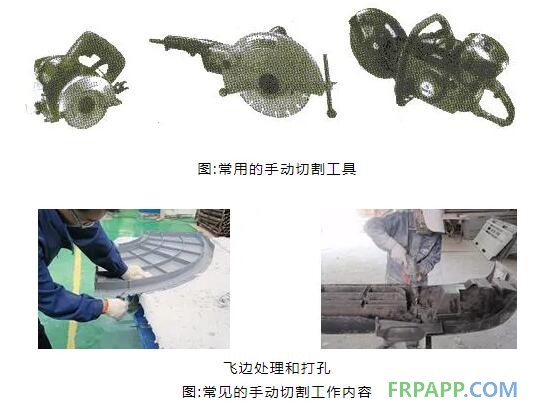
(b)機械切割
如圖為順切和逆切示意圖。在各種切割形式中,順切效果要比逆切效果好得多。原因在于:逆切時工件的進給方向與刀具的切割方向相反,刀具切入工件后,最終在A點切割上表面,使纖維首先被扯起,然后才撕開,從而在工作表面產(chǎn)生纖維隆起現(xiàn)象。順切時,工件的進給方向與刀具的旋轉(zhuǎn)方向一致。刀具在B點開始進入工件,顯然最上層材料受到向下壓的切割分力作用,因此,不會產(chǎn)生逆切時的纖維隆起。
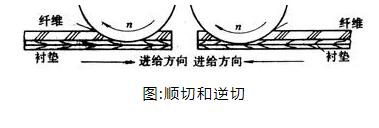
(c)高壓水射流切割技術
高壓水射流的原理是將水通過增壓器,使系統(tǒng)壓力增加到400MPa再由藍寶石噴嘴(孔直徑為0.2 mm )噴出,形成噴射速度高于音速的高壓切割水流,可對各種復合材料進行切割和開孔。高壓水射流切割的優(yōu)點:切縫窄、切割不發(fā)熱、無粉塵飛揚、工作環(huán)境不受污染、工件無變形等。高壓水射流一般分為高壓水射流和磨料水射流兩種。高壓水射流是指形成射流的工作介質(zhì)由水和磨料組成,其中水作為載體使磨料獲得足夠的動能,對被切割件進行磨削和沖蝕。其切割系統(tǒng)流程圖如圖43.33所示,高壓水射流切割設備圖如圖,切割范圍如表所示。
表:切割厚度范圍
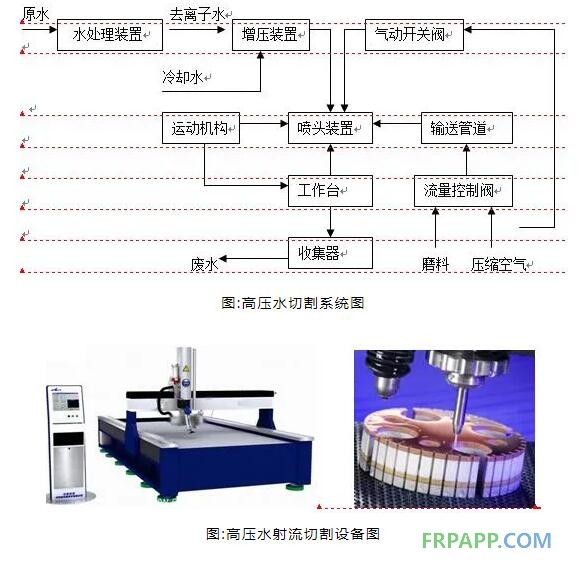
(2)打孔
在復合材料構件的連接中,機械連接占據(jù)著主要地位。當復合材料構件裝配時,需加工出許多緊固件孔。SMC打孔的方法主要有手槍鉆加工、數(shù)控加工中心加工和機器人加工。典型手槍鉆加工照片如圖43.35所示、數(shù)控加工中心照片如圖所示、機器人加工中心如圖所示。
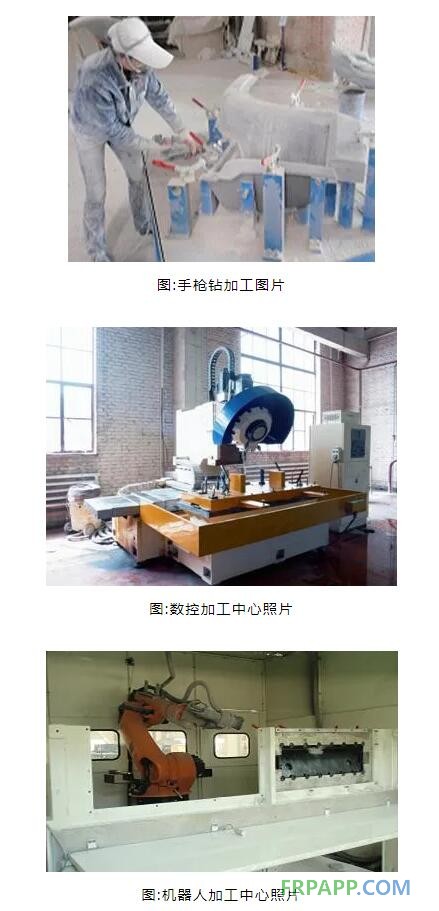
2.連接設計
通常用于金屬結構部件之間的兩種主要連接方法,即機械緊固件連接和膠接連接也適用于復合材料的連接。SMC/BMC與一般金屬材料的區(qū)別是:層間強度低、在連接部位的應力集中或應變集中嚴重,在此區(qū)域載荷重新分配的能力較弱。對復合材料的連接進行分析和正確設計,是保證結構連接成功的首要條件。
(1)聚酯模塑料機械連接技術
聚酯模塑料的機械連接方式一般有金屬螺紋及嵌件連接、螺栓(螺釘)連接、鉚接。聚酯模塑料的常用機械連接方式如圖所示。
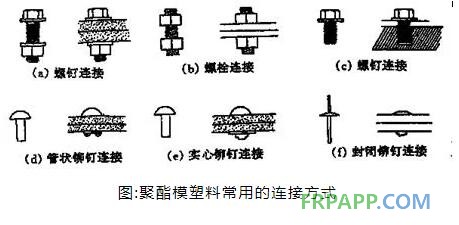
適用于聚酯模塑料的專用結構件,在安裝時必須滿足一些特殊要求。只有這樣,機械連接在復合材料結構中應用才有可能。
(a) 螺接工藝要求
① 緊固件與孔的配合,要求達到H8/f8,孔與板的垂直度偏差在2º以內(nèi)。
② 復合材料構件表面斜度超過5º時,必須使用特制傾斜度的墊圈。
③ 除傳力件外(如電纜導管夾子、墊板等),螺栓的螺紋部分不允許在孔的擠壓部位。
④ 在連接部位,特別在潮濕部位安裝緊固件,一律采用濕裝配。濕裝配時,孔內(nèi)或緊固件應涂密封膠,允許螺紋粘上密封膠,螺母必須在膠的施工期內(nèi)上緊完畢。
⑤ 多釘連接安裝時,不宜逐一的將單個螺栓一次擰緊,而應均衡對稱的將所有螺栓分若干次擰緊,直至達到規(guī)定的擰緊力矩值。對縫內(nèi)密封的螺栓,需分兩次擰緊,初次擰緊必須在密封劑活性期內(nèi)完成,重擰必須在初次擰緊后20分鐘內(nèi)進行,兩次擰緊需在密封材料施工期內(nèi)完成。
(2)鉚接工藝
由于復合材料層間強度低和抗沖擊能力差等弱點,一般認為不宜進行鉚接。但是在一些承力不大的部位上,在采取一定工藝措施后,鉚接工藝仍獲得較普遍的應用。按釘桿粗細情況的不同,可分為釘桿鐓粗的鉚接和釘桿局部變形的鉚接如半空心鉚釘及雙金屬鉚釘?shù)你T接。
①釘桿鐓粗的實心鉚釘鉚接工藝
在復合材料結構上應用最多的是TAl純鈦鉚釘。這種鉚釘在使用前,必須經(jīng)真空退火處理,使其降低強度、改善塑性。鉚接時,在鐓頭部位如為碳纖維復合材料,必須加厚度大于lmm純鉆墊圈。對直徑為d的純鈦鉚釘,鉚接復合材料的工藝參數(shù)如下:
鉚釘孔徑=d十(0.3~0.4)
墊圈直徑=d十(0.1~0.2)
鐓頭直徑=(1.3~1.5)d
鐓頭高度=(0.5~0.65)d
②釘桿局部變形的半空心鉚釘鉚接工藝
為避免釘桿過粗而造成基體孔壁損傷,國外研制了僅釘尾產(chǎn)生變形而主桿部分基本不膨脹的半空心鉚釘,它既使層合板牢固地連接在一起,又不使孔壁損傷,是一類很適于復合材料結構連接的新型緊固件。
半空心鉚釘有兩種型式:a雙面埋頭型半空心鉚釘,它的材料為退火的55Ti—45Nb,其抗剪強度達345MPa,承載能力較高,由于鉚接時釘?shù)闹鳁U不變形,所以鉚接力只等于鉚同樣材料實心鉚釘?shù)囊话耄饕m用在副翼、舵面、調(diào)整片等要求雙面埋頭的操縱面外部結構。b 凸頭型半空心鉚釘,材料為蒙乃爾合金,鉚接時在成型模的作用下形成帽形鐓頭,能有效地將構件連接在一起,它主要應用于內(nèi)部結構。
(2)聚酯模塑料膠接連接技術
膠接連接的主要優(yōu)點有 :不會因鉆孔引起應力集中和纖維切斷,不減少承載橫剖面面積;與連接形式相同的機械連接件比較,在受力較小的次要結構上,膠接連接件能夠減重約25%,在受力大的主要結構上,膠接連接件能夠減重5%~10%;能夠獲得平滑的結構表面,連接元件上的裂紋不易擴展,密封性較好;大面積膠接成本低;可用于不同材料之間的連接,無電偶腐蝕問題;加載后的永久變形較小;便于實現(xiàn)連接強度的優(yōu)化設計。
膠接連接的缺點有:連接元件表面需要仔細處理;強度分散性大,由于濕度、溫度等環(huán)境因素的影響,膠接強度會逐漸降低;對膠接質(zhì)量的無損探傷比較困難;在大多數(shù)情況下是不可拆卸的。
(a) 膠粘劑的選擇
復合材料的粘接要選用強度高、耐熱性好的膠粘劑。復合材料常用的膠粘劑有環(huán)氧膠、酚醛-縮醛膠、快固丙烯酸酯膠、α-氰基丙烯酸酯膠、聚氨基膠等。
(b)粘接接頭的設計
粘接接頭由被粘物與夾在之間的膠層構成,是結構部件上的不連續(xù)部分,起著傳遞應力的作用。接頭強度取決于膠粘劑的內(nèi)聚強度、被粘物本身的強度和膠粘劑與被粘物界面的結合強度。而實測強度主要由三者之中最薄弱環(huán)節(jié)所支配,還受接頭形式、幾何尺寸和加工質(zhì)量的影響。為使粘接的優(yōu)點得到充分發(fā)揮,而將其缺點盡量縮小,必須確定合理的粘接接頭結構。
接頭的形式很重要,因為有機膠粘劑的最佳使用效果,是用于承受單純或扭轉(zhuǎn)的剪切力。實際上應用的接頭形式可以是形式各異、變化多端,但總的都是幾種基本類型的單獨或相互組合的結果。圖列舉了幾種聚酯模塑料的典型粘接接頭形式。
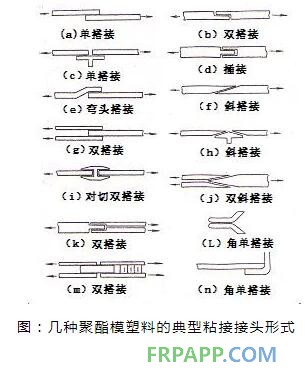
(c)膠接設備
圖:為常用的膠接設備。
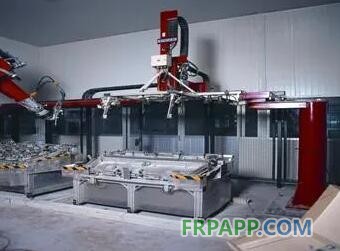
3.表面涂裝
聚酯模塑料制品的表面涂飾工藝,通常是指在聚氨酯模塑料制品成型后(有時是在成型中),使用各種各樣具有高性能的或特種功能的涂料,采用不同的涂裝方法,對聚酯模塑料制品的表面進行涂裝,從而起到裝飾、保護、協(xié)調(diào)或賦予新功能作用的一種工藝方法。在玻璃纖維增強塑料領域中,片狀模塑料(SMC)制品的涂裝工藝在世界上研究的最多、最充分。SMC涂裝工藝與普通的玻璃鋼制品相比也最復雜。下面主要從表面涂裝用原材料、表面涂裝工藝和表面涂裝設備三方面介紹SMC制品的涂裝工藝。
(1)表面涂裝用原材料
一般來說,典型的涂料系統(tǒng)由顏料,膠粘劑和溶劑組成。顏料提供顏色,耐久性和遮蓋能力;而膠粘劑分散顏料,也提供整體性,耐久性,柔韌性和粘接性能;溶劑的作用是為噴涂而調(diào)節(jié)粘度,在噴涂過程中大部分揮發(fā),留下的部分在漆膜固化時揮發(fā)干凈。在涂料中往往還加入一些特殊的添加劑,以改善它的固化和增加光澤等等。強化外觀的添加劑如金屬或云母薄片也可加入,以產(chǎn)生珍珠般的漆膜。
(a)樹脂性膠粘劑
通常也稱其為成膜劑,是涂料牢固地附著于被涂物面上形成連續(xù)漆膜的主要物質(zhì)。它是一種堅韌的、無定形的聚合物,賦予涂料大部分的熱,機械化學和耐候性能。某些膠粘劑是軟的和半彈性的如瀝青和橡膠類,而另外一些是比較堅硬的,有時還是脆性的如環(huán)氧類和丙烯酸類。
(b)溶劑
涂料中所用的溶劑是一種純的或混合的液體,它的主要作用是使膠粘劑或成膜劑溶解或分散成為粘稠的液體,以便涂料施工應用。溶劑的選用除了考慮其與膠粘劑的溶解性或分散性外,還需要注意其揮發(fā)性、毒性、閃點和價格等因素。
(c)顏料
涂料的顏料是在涂料中存在的小的實心的顆粒,它賦予涂層特殊的性能。顏料的顆粒尺寸范圍從1um以下到100um以上,它們的形狀可以是球形、片狀或針狀。顏料主要起裝飾和保護的作用,并改進涂料的應用性能和力學性能,如增加硬度、耐久性以及降低成本等。
(d)添加劑
添加劑有時也稱其為助劑。在涂料中,添加劑的用量是很少的,主要用于改善涂料某方面的性能。涂料用添加劑通常按其對液態(tài)涂料和涂料干燥后的涂層性能的影響進行分類,添加劑對液態(tài)涂料的下列重要性能有影響:如粘度、成膜性、結皮性、顏料分散性和乳液穩(wěn)定性等。添加劑也對典型的干漆膜性能的柔韌性(硬度)、光澤、光穩(wěn)定性和耐火焰等性能有影響。添加劑經(jīng)常以它的功能來命名,例如,消泡劑,分散劑,乳化劑,潤濕劑等。濕潤分散劑用來改善涂料在生產(chǎn)過程中的性能;防沉劑,防結皮劑等用來改善涂料的儲存穩(wěn)定性等;流平劑、增稠劑、防流掛劑、成膜助劑、UV吸收劑、阻燃劑、防靜電劑等用來改善涂膜的某些特殊性能。
下表中為常見的涂料類型:
下表中為常見的涂料類型:
(2)表面涂裝工藝
(a)噴涂工藝
SMC車身板的噴漆本質(zhì)上和其他材質(zhì)沒什么區(qū)別,也使用普通的噴漆室、固化烘房和靜電噴涂設備。粉末噴涂和水性涂料系統(tǒng),日益為人們所接受并使用,但是,溶劑型涂料的靜電噴涂仍是使用的主流、標準的方法。
a)涂料的靜電噴涂
大多數(shù)成型廠和組裝廠都比較愿意用靜電噴涂,因為這種工藝涂料使用量較少,最少的用量有利于成本和有機物的排放。在SMC底材上噴涂涂料層的一般程序是:導電底漆涂層→底漆→二道底漆涂層和BC/CC涂料層。
b)導電底漆涂層
導電底漆能促進對底材的粘接和為靜電噴涂面漆提供導電的表面。導電底漆通常是一種密胺/聚酯、密胺/醇酸樹脂或聚氨酯/多元醇,這些涂料在120~150℃范圍內(nèi)固化。SMC底漆涂料還可以配制成一種底材除氣作用的阻擋層,這有助于困于底材的空氣和水蒸氣而產(chǎn)生的漆層鼓泡減少到最小的程度。
c)磷化處理層和電泳底漆
磷化處理層可以減少在噴涂面漆之前產(chǎn)生另外的灰塵進入的可能性。即使SMC零件通過電泳底漆噴涂加工,但涂料不會粘在零件上。SMC經(jīng)過電泳底漆的最高溫度不要超過204℃,時間不要長于30min。
d)底漆-二道漆底漆
底漆-二道漆底漆提供優(yōu)良的充填細微空穴和擦傷缺陷的能力,它含有更多的固體,因而能形成厚的涂層而不會產(chǎn)生漆皺缺陷。
e)密封涂層
密封涂層是一種噴涂在底漆涂層和面漆層之間,以改善他們之間粘接的涂料膜。密封涂料像底漆涂料一樣有熱固性和熱塑性兩種類型,應和底漆涂料適當配合使用,例如:磁漆(熱固性)密封涂料會攻擊硝基漆(熱塑性)底漆涂料,因而他們不可復合使用。
f)SMC汽車件面漆
在制品上的最后的一層,肉眼可見的漆膜,這是面漆涂層。面漆涂層可以分幾次單獨噴涂,如果涂層不烘烤而僅僅閃蒸就開始進行下一次的噴涂,這就稱之為濕對濕涂敷。面漆涂層必須提供外表面理想的顏色、光澤、耐磨性和耐候性。
(b) 涂料的固化
所有經(jīng)過噴涂的零件,在固化的烘道(房)中至少要經(jīng)過3個單獨的加熱區(qū)進行固化:溫度躍升區(qū)、固化區(qū)和冷卻區(qū)。某些烘道設計還配備有附加的加熱和冷卻區(qū),以利用不同車身板的特殊的材料特性的優(yōu)勢。在這些噴涂系統(tǒng)中,零件在進入第一區(qū)之前可以先曝露在輻射熱的條件下,在這個輻射熱區(qū),零件經(jīng)受高達260℃的高溫長達8min。這種高的熱梯度會引起涂層粘度快速下降,從而有助于零件所有表面上涂料的流動(熔流)和變得平整。它也會導致涂層形成完整的表皮層,可以減少當零件通過烘道受灰塵污染的可能性。噴涂過的零件經(jīng)過輻射加熱區(qū)后,進入溫度躍升區(qū),零件溫度從室溫升到149℃,在該區(qū)停留10min;然后進入固化區(qū),在149℃下固化30min;最后,零件在冷卻區(qū)停留15min,溫度從149℃降到室溫。
(c)工藝流程
SMC制品的表面涂飾工藝流程與其他玻璃鋼制品的表面涂飾工藝流程相似,下圖為一常見的SMC汽車制品的表面涂飾工藝流程圖。
刮膩子→干燥→打磨→刮一遍膩子→干燥→打磨→水砂紙細磨→干燥→噴反光漆→干燥→噴透明面漆→干燥→貼花→罩光→干燥
(3)表面涂裝設備
SMC/BMC的噴涂設備和用于其他底材(如金屬)的設備沒有什么不同,絕大部分常規(guī)的噴涂設備,原則上都可以用于SMC/BMC的表面噴涂。當噴涂數(shù)量較小,而且品種經(jīng)常變換或者在多品種小批量的情況下,可以使用簡單的人工噴涂系統(tǒng)。而當某些產(chǎn)品具有較大規(guī)模的產(chǎn)量時,一般都要在單獨建立的噴漆生產(chǎn)線上進行噴涂。
(a)噴涂設備簡介
a) 常規(guī)的小規(guī)模噴涂系統(tǒng)
普通的工業(yè)噴涂系統(tǒng)是由空壓機、調(diào)節(jié)器、涂料罐和噴槍及空氣管線組成。其中噴槍是關鍵設備,普通的空氣噴涂噴槍主要有壓力型和吸入型兩種。壓力型噴槍一般用于需迅速供應大量涂料的場合,又分為空壓式和機械壓力式。吸入式噴槍用于多種顏色低產(chǎn)量間歇式生產(chǎn),涂料從直接連在噴槍上的涂料杯中吸取。典型的壓力喂入空氣噴槍是由空氣管線供應空氣以霧化涂料,涂料管線供應涂料。空氣噴涂的傳遞效率為15%-30%。
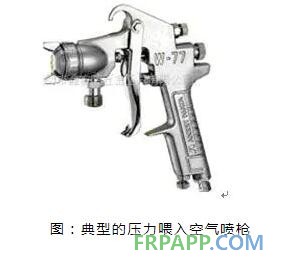
噴槍的另外一種類型就是無氣噴槍,它沒有空氣管線連接到槍體上。涂料在非常高的壓力下送到噴槍內(nèi)。典型的范圍為7-14MPa。無氣噴涂的傳遞效率是20%-40%。
b) 噴涂室
一般的噴涂外圍設備有三種主要類型,噴涂室、空氣供應系統(tǒng)和廢料處理裝置,其中主要的是噴涂室。噴涂室是包圍噴涂區(qū)的密封小屋,它的功能是防止漆霧外泄和保持噴涂過程中涂料不受灰塵的污染。
c) 靜電噴涂設備
靜電噴涂可以降低涂料的損耗。靜電噴涂實質(zhì)上是帶電的涂料液滴沿著在噴槍和零件之間的電力線移動形成涂層的過程。靜電噴涂和常規(guī)的空氣噴涂相比,同樣的涂料用量可多噴50%-70%的零件,尤其是對大而平的制品效率更高。靜電噴涂有更均勻的涂層厚度和更好的覆蓋邊角的能力,但對制品的凹陷部分不能實現(xiàn)良好的覆蓋。
(b)典型的噴涂生產(chǎn)線
在世界各國規(guī)模化的SMC制品噴涂生產(chǎn)線均以汽車噴涂生產(chǎn)線為其表率,它不僅代表SMC制品的噴涂及相關技術的最高水平,也是噴涂應用最廣泛的領域。下圖為某汽車件生產(chǎn)廠的噴涂線的平面布置圖。
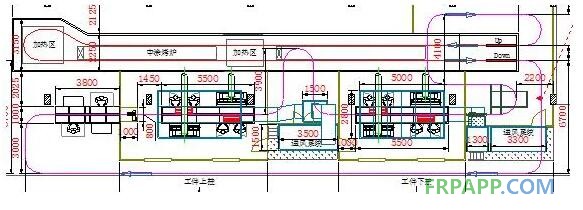