1 概 述
環(huán)氧樹脂基復(fù)合材料因具有比強(qiáng)度高、比模量大、結(jié)構(gòu)整體性好、可設(shè)計(jì)性強(qiáng)、耐疲勞性好、可修復(fù)性強(qiáng)及安全性好等優(yōu)點(diǎn)而應(yīng)用于航空產(chǎn)品結(jié)構(gòu)件上,但其缺陷是脆性大、韌性差和抗沖擊損傷容限低等。隨著復(fù)合材料廣泛地應(yīng)用,特別是應(yīng)用于航空產(chǎn)品上,提高復(fù)合材料的韌性一直是國內(nèi)外復(fù)合材料領(lǐng)域所關(guān)注的問題。目前普遍采用沖擊后壓縮強(qiáng)度CAI值來表征復(fù)合材料的韌性。一般認(rèn)為沖擊能為6. 7J/m2時(shí), CAI值在193MPa以下為低韌性復(fù)合材料; 193~255MPa為韌性復(fù)合材料;大于255MPa為高韌性復(fù)合材料1。為提高復(fù)合材料韌性,國內(nèi)外研究人員進(jìn)行了大量的工作。
由洪都航空工業(yè)集團(tuán)自行研制的NY9200G環(huán)氧樹脂體系制成的先進(jìn)樹脂基復(fù)合材料自1996年通過中國航空工業(yè)總公司鑒定以來,已用于某飛機(jī)結(jié)構(gòu)件上,并投入批生產(chǎn),取得了明顯的技術(shù)和經(jīng)濟(jì)效益。實(shí)踐證明:該樹脂體系是一種工藝性好、技術(shù)成熟、性能優(yōu)良及價(jià)格便宜的環(huán)氧樹脂復(fù)合材料基體。但隨著新型號對復(fù)合材料韌性要求的不斷提高,與韌性復(fù)合材料相比,其沖擊后壓縮強(qiáng)度CAI值相對韌性復(fù)合材料CAI值193~255MPa有一定的差距。為進(jìn)一步提高環(huán)氧樹脂基復(fù)合材料的韌性,以NY9200G/T300環(huán)氧樹脂體系為基礎(chǔ),開展提高環(huán)氧樹脂基復(fù)合材料韌性的研究是完全必要的。
在環(huán)氧樹脂基復(fù)合材料增韌方面,國內(nèi)外的研究方向主要集中在以下三個(gè)方面:
1)在樹脂基體中加入增韌劑,主要是加入液體橡膠。此項(xiàng)工作自六十年代以來一直在進(jìn)行,取得了一定的進(jìn)展。但液體橡膠在提高復(fù)合材料韌性的同時(shí),也降低了其它物理機(jī)械性能。
2)在樹脂體系中加入擴(kuò)鏈劑,使環(huán)氧樹脂分子首先為線形增長,然后再聚合,得到更大的聚合物,以提高復(fù)合材料的韌性。
3)從工藝上提高樹脂基復(fù)合材料的韌性。如采用“離位”增韌技術(shù)提高復(fù)合材料的韌性。針對上述三種增韌方法,經(jīng)過分析,我們確定采用第三種方法,即從工藝上提高樹脂基復(fù)合材料的韌性,結(jié)合正在某飛機(jī)結(jié)構(gòu)件上使用的NY9200G/T300環(huán)氧樹脂體系,采用“離位”增韌技術(shù)提高NY9200G/T300復(fù)合材料的韌性。所謂“離位”,從復(fù)合原理上講,就是將復(fù)相增韌技術(shù)中的增韌相從基體中分離,讓它單獨(dú)與增強(qiáng)相復(fù)合,在不改變原有熱固性預(yù)浸料所有工藝優(yōu)點(diǎn)并保持其面內(nèi)力學(xué)性能的同時(shí),大幅度提高了復(fù)合材料的沖擊損傷阻抗,并兼顧了低制備成本2。其形成的雙連續(xù)的3-3結(jié)構(gòu)作為高效的增韌微結(jié)構(gòu),大大提高了層間剪切強(qiáng)度、GⅠC、GⅡC和抗沖擊損傷性能,從而達(dá)到增韌效果。該增韌方法既不改變其原體系中的固化反應(yīng)歷程又不改變固化物的化學(xué)結(jié)構(gòu),是一種在工藝過程中加入增韌物的物理增韌方法。在研究過程中,采用“離位”增韌技術(shù)對NY9200G/T300環(huán)氧樹脂體系復(fù)合材料進(jìn)行增韌,通過常規(guī)力學(xué)性能試驗(yàn)、韌性性能試驗(yàn)、螺接擠壓強(qiáng)度試驗(yàn)和加筋板研制及其沖擊后疲勞靜強(qiáng)度試驗(yàn),將其與未增韌的NY9200G/T300環(huán)氧樹脂體系復(fù)合材料性能進(jìn)行比較,考核“離位”增韌技術(shù)的增韌效果,從而得出結(jié)論。同時(shí),摸索“離位”增韌技術(shù)成型工藝,考核驗(yàn)證其結(jié)構(gòu)件功能,以期大幅度提高該復(fù)合材料沖擊后壓縮強(qiáng)度CAI值。
本研究完成后已實(shí)現(xiàn)下列主要技術(shù)目標(biāo):
1)在基本保持NY9200G/T300復(fù)合材料力學(xué)性能和工藝性能的同時(shí),“離位”技術(shù)增韌的NY9200GES/T300復(fù)合材料沖擊后壓縮強(qiáng)度CAI值平均達(dá)到260MPa。
2)采用“離位”增韌技術(shù),不僅不會(huì)降低NY9200G/T300復(fù)合材料的螺接擠壓強(qiáng)度,而且還使其略有提高。
3)按典型鋪層研制的加筋板,采用“離位”增韌技術(shù),沖擊后疲勞靜強(qiáng)度高于同時(shí)制備的同種未增韌加筋板。
2 試驗(yàn)部分
2. 1 NY9200GES/T300“離位”增韌預(yù)浸料的制備
采用“離位”增韌技術(shù),對NY9200G/T300環(huán)氧樹脂體系進(jìn)行增韌,得到NY9200GES/T300“離位”增韌預(yù)浸料。
2. 2 NY9200GES /T300“離位”增韌預(yù)浸料的固化工藝參數(shù)NY9200GES/T300“離位”增韌預(yù)浸料的固化工藝參數(shù)同NY9200G/T300環(huán)氧樹脂體系,即:先升溫至130±5℃,保溫30~35min后,再加外壓≥0. 5Mpa,然后升溫至175~180℃,保溫2~2. 5h。
2. 3 “離位”增韌復(fù)合材料的韌性性能和常規(guī)力學(xué)性能試驗(yàn)
NY9200GES/T300增韌復(fù)合材料韌性性能和常規(guī)力學(xué)性能的測試均按目前先進(jìn)復(fù)合材料行業(yè)通行采用的國標(biāo)或相應(yīng)的標(biāo)準(zhǔn)進(jìn)行,具體標(biāo)準(zhǔn)見表1和表2。所需試板均在同一熱壓罐內(nèi)同一批次固化成型,固化工藝參數(shù)同NY9200G/T300環(huán)氧樹脂體系。NY9200G/T300環(huán)氧樹脂復(fù)合材料的韌性性能和常溫常規(guī)力學(xué)性能以公開發(fā)行的中國航空材料手冊第6卷(復(fù)合材料)中的數(shù)據(jù)為準(zhǔn),以此為基礎(chǔ)作為試驗(yàn)的空白樣,兩者測試標(biāo)準(zhǔn)一致。(NY9200GES/T300增韌復(fù)合材料韌性性能和常規(guī)力學(xué)性能的測試由北京航空材料研究院完成。)
2. 4 復(fù)合材料螺接擠壓強(qiáng)度試驗(yàn)
選定的螺接擠壓強(qiáng)度試樣為φ6單釘雙剪和φ5雙釘單剪(包括沉頭和平頭)兩種,試樣材料分別為NY9200G/T300和NY9200GES /T300復(fù)合材料層壓板,鋪層順序均為[±45/(0)2/±45/90/±45/(0)2/90],鋪層比例都為40/50/10。(螺接擠壓強(qiáng)度試驗(yàn)在中國飛機(jī)強(qiáng)度研究所完成。)
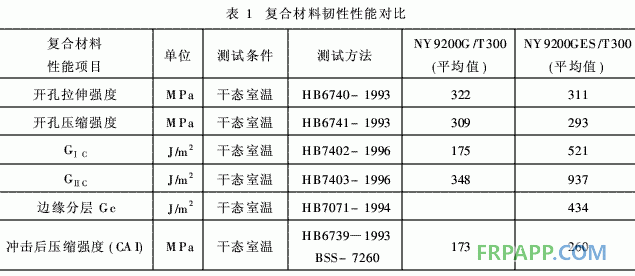
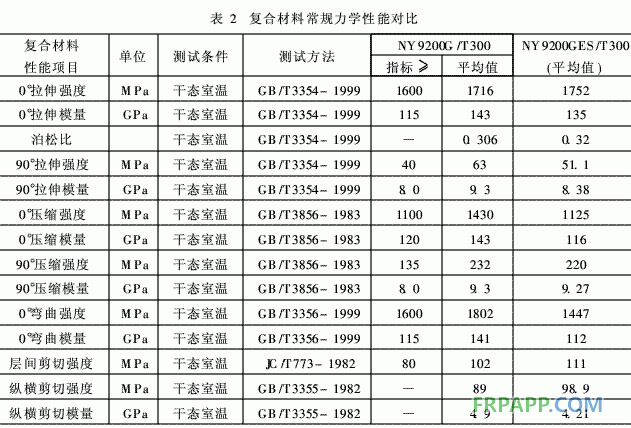
2. 5 加筋板的研制及其性能試驗(yàn)
為全面考核“離位”技術(shù)對NY9200G/T300復(fù)合材料增韌的效果,按增韌方法研制1件加筋板,見附圖。該加筋板是按某型號飛機(jī)垂尾翼盒根部碳纖維鋪層、比例縮小的模擬垂尾盒段件,我們對其進(jìn)行沖擊后疲勞靜強(qiáng)度試驗(yàn)。同時(shí)制備1件未增韌的同種加筋板進(jìn)行沖擊后疲勞靜強(qiáng)度試驗(yàn),并將試驗(yàn)結(jié)果進(jìn)行比較。(加筋板沖擊后疲勞靜強(qiáng)度試驗(yàn)在中國飛機(jī)強(qiáng)度研究所完成。)
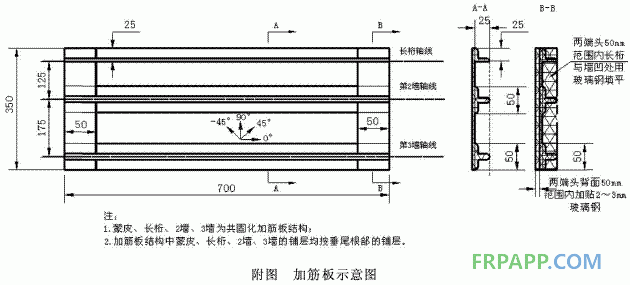
3 結(jié)果及討論
3. 1 NY9200GES/T300增韌復(fù)合材料的韌性性能
復(fù)合材料的韌性一般采用開孔拉伸強(qiáng)度、開孔壓縮強(qiáng)度、沖擊后壓縮強(qiáng)度、邊緣分層層間斷裂韌性、Ⅰ型層間斷裂韌性和Ⅱ型層間斷裂韌性來表征,其中沖擊后壓縮強(qiáng)度CAI值是目前國際上通行評價(jià)韌性高低最常用的性能指標(biāo)。
以NY9200G/T300復(fù)合材料性能數(shù)據(jù)為空白樣作為對比基礎(chǔ),“離位”技術(shù)增韌的NY9200GES/T300復(fù)合材料韌性性能見表1。
“離位”技術(shù)增韌的復(fù)合材料開孔拉伸強(qiáng)度及開孔壓縮強(qiáng)度與未增韌復(fù)合材料相當(dāng)。而GⅠC,GⅡC性能值則有大幅度提高。
“離位”技術(shù)增韌的復(fù)合材料沖擊后壓縮強(qiáng)度CAI值260MPa較未增韌復(fù)合材料173MPa有極大地提高,為未增韌復(fù)合材料的150. 3%。
3. 2 NY9200GES/T300增韌復(fù)合材料的常規(guī)力學(xué)性能
常規(guī)力學(xué)性能可以全面反映復(fù)合材料的基本性能,是復(fù)合材料結(jié)構(gòu)設(shè)計(jì)的依據(jù)。復(fù)合材料的常規(guī)力學(xué)性能主要包括: 0°拉伸強(qiáng)度、0°拉伸模量、泊松比、90°拉伸強(qiáng)度、90°拉伸模量、斷裂伸長率、0°壓縮強(qiáng)度、0°壓縮模量、90°壓縮強(qiáng)度、90°壓縮模量、層間剪切強(qiáng)度、彎曲強(qiáng)度、彎曲模量、縱橫剪切強(qiáng)度和模量等。
“離位”技術(shù)增韌的復(fù)合材料常規(guī)力學(xué)性能見表2,此表以NY9200G/T300復(fù)合材料性能數(shù)據(jù)為空白樣作為對比基礎(chǔ)。
0°拉伸性能試驗(yàn)結(jié)果表明:采用“離位”技術(shù)增韌的NY9200GES/T300復(fù)合材料0°拉伸性能與NY9200G/T300復(fù)合材料基本相當(dāng),并且高于其指標(biāo)值。
90°拉伸性能主要反映復(fù)合材料的樹脂基體內(nèi)聚強(qiáng)度和樹脂與纖維間的界面粘接強(qiáng)度。從表2數(shù)據(jù)可以看出:“離位”技術(shù)增韌的NY9200GES/T300復(fù)合材料90°拉伸強(qiáng)度和模量均高于NY9200G/T300復(fù)合材料指標(biāo)值。
0°壓縮性能試驗(yàn)結(jié)果表明:“離位”技術(shù)增韌的NY9200GES /T300復(fù)合材料的0°壓縮強(qiáng)度和模量與NY9200G/T300復(fù)合材料指標(biāo)值相當(dāng)。
90°壓縮性能試驗(yàn)結(jié)果表明:“離位”技術(shù)增韌的NY9200GES/T300復(fù)合材料的90°壓縮強(qiáng)度和模量均與NY9200G/T300復(fù)合材料相當(dāng),并且遠(yuǎn)高于其指標(biāo)值。
0°彎曲性能在表觀上顯示:“離位”增韌復(fù)合材料的彎曲強(qiáng)度及模量均有一定程度的下降。實(shí)際上,正常斷口情況下彎曲性能主要由纖維控制,當(dāng)纖維體積含量較低時(shí),彎曲強(qiáng)度和模量均有不同程度下降??紤]到“離位”增韌復(fù)合材料試樣纖維體積含量較低,可以認(rèn)為:當(dāng)“離位”增韌復(fù)合材料與未增韌復(fù)合材料的纖維體積含量相當(dāng)時(shí),兩者彎曲性能應(yīng)基本相當(dāng)。
層間剪切強(qiáng)度是反映樹脂基復(fù)合材料基體內(nèi)聚強(qiáng)度及其與纖維之間粘接強(qiáng)度的一個(gè)重要指標(biāo),層間剪切強(qiáng)度的高低直接影響到樹脂基復(fù)合材料的承載能力。從表2數(shù)據(jù)來看:“離位”技術(shù)增韌的NY9200GES/T300復(fù)合材料層間剪切強(qiáng)度高于NY9200G/T300復(fù)合材料,并且遠(yuǎn)高于其指標(biāo)值。
縱橫剪切性能試驗(yàn)結(jié)果表明:“離位”技術(shù)增韌的NY9200GES /T300復(fù)合材料的縱橫剪切性能與NY9200G/T300復(fù)合材料相當(dāng)。
綜上所述,我們可以得出:“離位”技術(shù)增韌的NY9200GES/T300復(fù)合材料基本保持了NY9200G/T300復(fù)合材料的常溫常規(guī)力學(xué)性能。
3. 3 復(fù)合材料螺接擠壓強(qiáng)度
從表3的數(shù)據(jù)來看,經(jīng)過“離位”技術(shù)增韌的復(fù)合材料螺接結(jié)構(gòu),其擠壓強(qiáng)度比未增韌的復(fù)合材料略高:對于φ5雙釘單剪試件,無論是平頭連接形式還是沉頭連接形式,“離位”增韌復(fù)合材料的極限擠壓強(qiáng)度均高于未增韌復(fù)合材料,但拐點(diǎn)擠壓強(qiáng)度則基本相當(dāng)。對于平頭連接形式,“離位”增韌復(fù)合材料的拐點(diǎn)擠壓強(qiáng)度和極限擠壓強(qiáng)度分別為547MPa和674MPa,而未增韌復(fù)合材料則分別為547MPa和606MPa,其極限擠壓強(qiáng)度的提高幅度為11. 2%;對于沉頭連接形式,“離位”增韌復(fù)合材料的拐點(diǎn)擠壓強(qiáng)度和極限擠壓強(qiáng)度分別為526MPa和664MPa,而未增韌復(fù)合材料則分別為518MPa和632MPa,其極限擠壓強(qiáng)度的提高幅度為5. 1%。對于φ6單釘雙剪試件,“離位”增韌復(fù)合材料的拐點(diǎn)擠壓強(qiáng)度和極限擠壓強(qiáng)度分別為883MPa和1004MPa,而未增韌復(fù)合材料的拐點(diǎn)擠壓強(qiáng)度和極限擠壓強(qiáng)度則分別為855MPa和993MPa,“離位”增韌復(fù)合材料的擠壓強(qiáng)度比未增韌復(fù)合材料略有提高。
實(shí)際上,“離位”增韌技術(shù)本身并沒有提高復(fù)合材料螺接擠壓強(qiáng)度的任務(wù),該試驗(yàn)的主要目的是為了考核“離位”增韌技術(shù)對NY9200G/T300復(fù)合材料螺接擠壓強(qiáng)度的影響。試驗(yàn)結(jié)果表明:“離位”增韌技術(shù)不但不會(huì)降低NY9200G/T300復(fù)合材料螺接擠壓強(qiáng)度,而且還使之略有提高?!?/p>
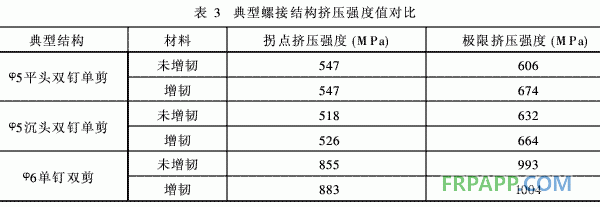
3. 4 加筋板的研制及其性能
3. 4. 1 加筋板的研制
“離位”增韌加筋板的成型步驟為:NY9200GES/T300“離位”增韌預(yù)浸料的制備→鋪貼蒙皮→預(yù)吸膠→鋪貼蒙皮→預(yù)固化→無損檢測→蒙皮與墻及長桁組裝→總固化→無損檢測→“離位”增韌加筋板。同時(shí)制備1件同種未增韌的加筋板,成型步驟同上。2件加筋板經(jīng)無損檢測均符合要求。
3. 4. 2 加筋板的性能
3. 4. 2. 1 “離位”增韌加筋板與未增韌加筋板的損傷阻抗性能
對于相同支持條件下且凹坑深度相近的情況下,“離位”增韌加筋板的損傷阻抗性能高于未增韌加筋板,具體結(jié)果如下:
a)在中跨蒙皮產(chǎn)生1. 2mm深凹坑時(shí),增韌加筋板承受的壓縮載荷為5. 52kN,而未增韌加筋板所承受的壓縮載荷僅為4. 73kN,“離位”增韌后的加筋板承載能力提高了16. 7%,而損傷面積卻減小了38. 8%;
b)在筋條凸緣邊緣處的蒙皮產(chǎn)生1. 2mm深凹坑時(shí),增韌加筋板承受的壓縮載荷為7. 92kN,而未增韌加筋板所承受的壓縮載荷僅為5.69kN,“離位”增韌后的加筋板承載能力提高了39.2%。
3. 4. 2. 2 疲勞試驗(yàn)中的損傷擴(kuò)展?fàn)顩r
疲勞試驗(yàn)前后,“離位”增韌加筋板與未增韌加筋板內(nèi)部損傷的無損檢測結(jié)果表明: 2倍疲勞壽命后,損傷都沒有發(fā)生擴(kuò)展。
3. 4. 2. 3 “離位”增韌加筋板與未增韌加筋板對壓縮強(qiáng)度的影響 從表4可以看到:對于包含中跨蒙皮損傷(相同凹坑深度)的加筋板,增韌加筋板的承載能力大于未增韌加筋板的承載能力,即加筋板B1比A1的初始屈曲載荷和極限承載能力分別提高了37. 5%和25%。
對于包含筋條凸緣處蒙皮損傷的加筋板,即使增韌加筋板的凹坑深度明顯大于未增韌加筋板,其承載能力也大于未增韌加筋板的承載能力,即加筋板B2比A2的初始屈曲載荷和極限承載能力分別提高了7. 2%和18. 6%?! ?/p>
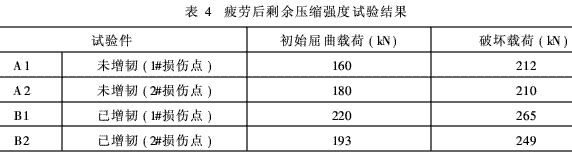
考慮到增韌加筋板與未增韌加筋板幾何尺寸的差異:增韌加筋板的蒙皮及L型筋條腹板的厚度均大于未增韌加筋板(蒙皮厚度增加了25. 9%,筋條腹板厚度增加了48. 2% ),在試件幾何尺寸存在較大差異的情況下,雖然已增韌加筋板表現(xiàn)出較高的承載能力,但不能由此判斷增韌對結(jié)構(gòu)承載能力的影響程度。然而,加筋板的破壞應(yīng)變(包括屈曲應(yīng)變和極限應(yīng)變)卻是一個(gè)與結(jié)構(gòu)厚度無關(guān)的無量綱參數(shù),同時(shí)也是結(jié)構(gòu)設(shè)計(jì)時(shí)應(yīng)考慮的重要指標(biāo)。因此,應(yīng)該以破壞應(yīng)變來考核復(fù)合材料的增韌效果,表5給出了增韌與未增韌加筋板破壞時(shí)蒙皮的應(yīng)變值。
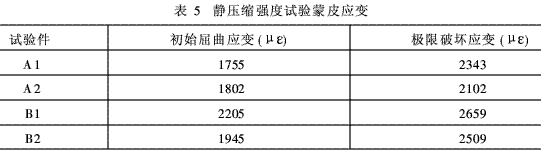
試驗(yàn)結(jié)果表明:
a)對于包含中跨蒙皮損傷(相同凹坑深度)的加筋板,增韌加筋板的破壞應(yīng)變大于未增韌加筋板,即加筋板B1比A1的初始屈曲應(yīng)變和極限應(yīng)變分別提高了25. 6%和13. 5%。
b)對于包含筋條凸緣處蒙皮損傷的加筋板,即使增韌加筋板的凹坑深度明顯大于未增韌加筋板,其承載能力也大于未增韌加筋板的承載能力,即加筋板B2比A2的初始屈曲載荷和極限承載能力分別提高了7. 9%和19. 4%。
綜上所述,可以得出:“離位”增韌加筋板的損傷阻抗高于未增韌加筋板;對于增韌與未增韌加筋板,損傷在2倍疲勞壽命期間均未擴(kuò)展;“離位”增韌提高了加筋板的承載能力(破壞應(yīng)變)。
4 結(jié) 論
1)“離位”技術(shù)增韌的NY9200GES/T300復(fù)合材料在基本不降低NY9200G/T300復(fù)合材料常溫常規(guī)力學(xué)性能的同時(shí),能顯著提高原體系復(fù)合材料的抗沖擊損傷能力、大幅度提高沖擊后壓縮強(qiáng)度CAI值,增韌效果顯著。
2)經(jīng)過“離位”技術(shù)增韌,NY9200G/T300復(fù)合材料螺接結(jié)構(gòu)的擠壓強(qiáng)度沒有降低,而且還略有提高。
3)“離位”技術(shù)增韌加筋板的損傷阻抗高于未增韌加筋板;對于增韌和未增韌加筋板,損傷在2倍疲勞壽命期間均未擴(kuò)展;“離位”增韌技術(shù)提高了加筋板的承載能力(破壞應(yīng)變)。