1 實(shí)驗(yàn)部分
1.1 實(shí)驗(yàn)原料
鄰甲酚醛環(huán)氧樹(shù)脂:JF-45,無(wú)錫樹(shù)脂廠;JECN-801:江山江環(huán)化學(xué)工業(yè)有限公司;CYD:巴陵石化公司;聯(lián)苯型環(huán)氧樹(shù)脂:自制;球形硅微粉:2μm,3μm,5μm,10μm,20μm,浙江通達(dá)威鵬電氣有限公司;硅烷偶聯(lián)劑:KH-560,武大有機(jī)硅新材料股份有限公司。
1.2 實(shí)驗(yàn)儀器
旋轉(zhuǎn)流變儀: Physica MCR301,奧地利AntonPaar;高速混合機(jī):10L,張家港輕工機(jī)械廠;開(kāi)放式塑煉機(jī):SK-160,上海橡膠機(jī)械廠;注壓機(jī):XS-ZY-100T,無(wú)錫旭升橡膠機(jī)械有限公司。
1.3 樣品制備
先進(jìn)行硅微粉的表面處理,將計(jì)量后的硅微粉和硅烷偶聯(lián)劑放入高速混合機(jī)中,每次高速混合1 min,靜置1 min,連續(xù)混合三次,然后再加入其它的組分以同樣的方式進(jìn)行混合,以提高混合效果和防止混合溫度升高?;旌虾蟮奈锪显陔p輥開(kāi)煉機(jī)上混煉,溫度為90℃~110℃,混煉時(shí)間3 min~5 min,輥速比1∶1·2(前∶后)。雙輥開(kāi)煉后冷卻,經(jīng)粉碎,然后過(guò)孔徑為0·154 mm的篩網(wǎng)(100 mesh),進(jìn)行測(cè)試。
1.4 測(cè)試
熔融黏度采用旋轉(zhuǎn)流變儀進(jìn)行,主機(jī)型號(hào)PhysicaMCR301,控溫系統(tǒng)為P-PTD200,測(cè)試系統(tǒng)為PP25平行平板,間隙0.5mm,測(cè)試溫度150℃,剪切速率掃描1 s-1~100 s-1,數(shù)據(jù)點(diǎn)8Pt./dec。
2 結(jié)果與討論
2.1 幾種基體環(huán)氧樹(shù)脂黏度對(duì)比
黏度對(duì)于聚合物的加工性有很大的影響,因此環(huán)氧樹(shù)脂的熔融黏度是環(huán)氧樹(shù)脂的重要性能指標(biāo)之一。低熔融黏度可以降低封裝材料的內(nèi)應(yīng)力,使其具有高的填充性和可操作性,使封裝器件具有高的可靠性。本文使用Physica MCR301型旋轉(zhuǎn)流變儀考察了三種ECN和TMBP及其不同比例混合物在150℃時(shí)的熔體黏度,結(jié)果見(jiàn)Fig.1,Fig.2所示。

從Fig.1可以看出,巴陵石化的鄰甲酚醛環(huán)氧樹(shù)脂在150℃時(shí)的熔融黏度最高,約為1 Pa·s,江環(huán)化工公司的ECN最低,約0.7 Pa·s,而無(wú)錫樹(shù)脂廠的鄰甲酚醛環(huán)氧樹(shù)脂熔融黏度約0·8 Pa·s,與江環(huán)化工公司的ECN黏度相差不大。同時(shí)從Fig.1還可以看出,三種ECN的熔融黏度隨剪切速率的變化趨勢(shì)是一致的,即隨著剪切速率的增大,黏度下降很少,表現(xiàn)為近似牛頓流體行為。
從Fig.2可以看出,TMBP的熔融黏度極低,在150℃時(shí)約為0·02 Pa·s,而剪切速率對(duì)TMBP黏度的影響比對(duì)ECN的影響稍大一些,呈現(xiàn)假塑性流體行為。同時(shí)可以發(fā)現(xiàn),隨著TMBP在ECN/TMBP共混物中的比例增大,熔融黏度也逐漸降低。TMBP含量40%時(shí)(質(zhì)量分?jǐn)?shù),下同),熔融黏度降到0·15 Pa·s。因此可以采用TMBP來(lái)降低ECN的黏度,從而達(dá)到提高復(fù)合材料流動(dòng)性的目的。
2.2 硅微粉填充量對(duì)黏度的影響
環(huán)氧模塑料中采用硅微粉作為填料,并且在環(huán)氧模塑料中含量高達(dá)60%~90%。硅微粉的主要作用是提高熱導(dǎo)率,降低熱膨脹系數(shù)和成型收縮率,還起到增強(qiáng)作用,提高可靠性。但同時(shí)會(huì)導(dǎo)致模塑料的黏度增加,降低成型性,所以填充量要選擇適當(dāng)。不同硅微粉填充量對(duì)環(huán)氧樹(shù)脂體系熔融黏度的影響如Fig.3所示。
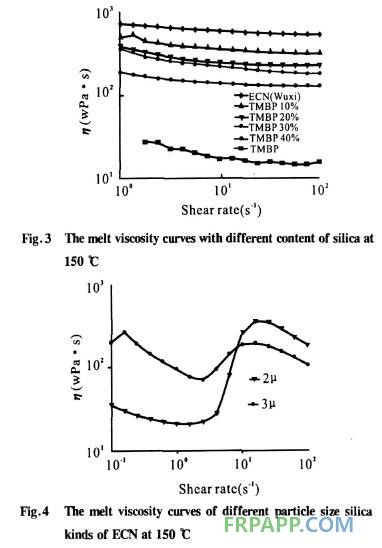
從Fig.3可以看出,硅微粉填充量為60%的ECN環(huán)氧樹(shù)脂體系熔融黏度約為11·2 Pa·s(.γ=10 s-1),填充量為70%的ECN環(huán)氧樹(shù)脂體系熔融黏度為144·9 Pa·s(.γ=10 s-1),黏度提高了10倍,可見(jiàn)增大硅微粉含量對(duì)體系的黏度影響很大。同時(shí),隨著剪切速率的增大,硅微粉含量為60%和70%的體系黏度變化趨勢(shì)較為相似。低含量的體系(硅微粉60%)表現(xiàn)為脹塑性流體行為(但仍然近似牛頓流體行為),而高含量的體系(硅微粉70%)黏度變化趨勢(shì)較復(fù)雜,先是在低剪切速率下呈現(xiàn)剪切變稀(假塑性流體)行為,而后在稍高的剪切速率下又表現(xiàn)為剪切變稠(脹塑性流體)行為,但在更高的剪切速率下,又變?yōu)榧偎苄粤黧w??梢?jiàn)剪切速率對(duì)高硅微粉填充量環(huán)氧樹(shù)脂模塑料體系的熔融黏度影響較為復(fù)雜,這就要求集成電路的封裝工藝制定要科學(xué)和仔細(xì)。
2.3 硅微粉粒徑對(duì)黏度的影響
硅微粉的顆粒粒徑一般在0·1μm~70μm范圍內(nèi),中位粒徑d50=1μm~20μm。不同粒徑硅微粉對(duì)環(huán)氧樹(shù)脂體系熔融黏度的影響如Fig.4所示。從Fig.4可以看出,剪切速率對(duì)不同粒徑硅微粉填充后體系的熔融黏度影響較大。低剪切速率下(6 s-1),兩種體系均呈現(xiàn)“剪切變稠”現(xiàn)象,而且粒徑為2μm硅微粉填充體系的熔融黏度大大增加比粒徑為3μm的體系黏度大。從Fig.4還可以看出小粒徑的硅微粉填充體系,在低剪切速率下黏度小,在高剪切速率下黏度大,而大粒徑的硅微粉正好與此相反。因此對(duì)不同的封裝工藝,要填充不同粒徑的硅微粉。
3 結(jié)論
聯(lián)苯型環(huán)氧樹(shù)脂TMBP熔融黏度極低(0·0Pa·s,150℃),用TMBP與鄰甲酚醛環(huán)氧樹(shù)脂共混,可大大降低體系的黏度,從而提高硅微粉的填充量和大規(guī)模集成電路封裝材料的流動(dòng)性。同時(shí)隨著硅微粉含量的增加,體系的熔融黏度大大增加。對(duì)高含量的硅微粉填充體系,隨著剪切速率的變化,其熔融黏度呈現(xiàn)復(fù)雜的變化趨勢(shì),即在低剪切速率下,呈現(xiàn)“剪切變稀”的現(xiàn)象,在較高剪切速率下呈現(xiàn)“剪切變稠”現(xiàn)象,而在高剪切速率下又表現(xiàn)為“剪切變稀”行為;而且小粒徑硅微粉填充體系在低剪切速率下黏度小,而在高剪切速率下黏度大,大粒徑硅微粉填充體系正好與此相反。