在材料大作戰(zhàn)的過程中,汽車行業(yè)的生產模式、供應商模式和組織結構都發(fā)生了變化。
11月26日,中國電動汽車百人會召開第七次電動汽車熱點問題研討會,議題為“電動汽車的輕量化”。來自政府、行業(yè)學會、高校和企業(yè)的100余名嘉賓參與了討論,中國電動汽車百人會理事長陳清泰對研討會進行了總結發(fā)言。車云菌將會議核心信息整理如下。

汽車輕量化的意義
從市場、汽車設計的角度,也許需要的是一個大車,一個豪華車,但是清華大學教授周青表示,從技術和汽車工程的角度,小型化和輕量化才有意義。輕量化不僅可以幫助節(jié)能減排,而且能提升車輛使用效率和行車安全。
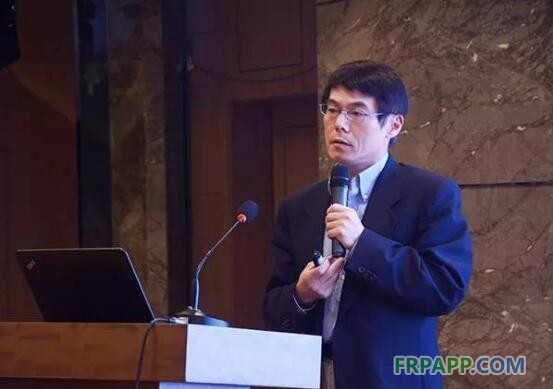
△清華大學教授周青
汽車輕量化與節(jié)能減排存在直接關聯。根據相關政策,到2020年,車企平均油耗必須降低到每百公里5升。工業(yè)和信息部原材料工業(yè)司副司長潘愛華介紹,統(tǒng)計估測,汽車整車重量減少10%,就能節(jié)油6%到8%,油耗能夠下降每百公里0.3到0.6升,氧化碳排放降低5~8克。
而對于新能源汽車而言,因為凈增電池重量達到了300Kg以上,因此輕量化更是必不可少的課題。周青表示,目前電動車電池能量密度提高困難,直到電池或者儲能裝置可以達到今天汽油,氫燃料的能量密度,才可能比較任意地按照今天的原理設計汽車。所以我們必須在現有電池能量密度的情況下,把車設計得更小更輕,從而增加電動車的續(xù)航里程,提升它的能量利用率。
一個明顯的現象是,目前路上家用汽車的空間利用率仍然很低。行車時只有一名乘員,大部分時間車輛被閑置在停車場,從這個角度來看,更小更輕的車更加能滿足使用效率。
從安全角度來看,輕量化和小型化可以令車更加安全。2000年前后美國聯邦政府交通部研究的一個結論顯示,如果能夠降低道路車輛的平均重量,能減少道路凈傷亡。并且隨著主動安全越來越發(fā)達,又小又輕的車更容易控制,在與行人和自行車碰撞時,造成的傷害也會降低。
汽車輕量化的三個途徑
汽車輕量化有三個途徑,一個是結構設計的優(yōu)化,一個是使用輕量化材料,還有一個是輕量化材料的成型技術。
1.結構設計優(yōu)化
在電動車輕量化的談論中,如何圍繞電池減重是一個被多次提到的話題。電池組在車里相當大的部件,空間和重量都很大,設計結構時一定會關注電池的排布。同時根據碰撞時受到什么樣的工況,以此評估電池風險。安全和減重是結構設計時需要平衡的天平兩端。
周青提出,電動車電池的安全設計目標是不著火,而不是不變形。為了不讓電池變形,只能增加很多結構和材料。電池本身可以承受一定的沖擊和變形,設計時主要應該考慮電池的碰撞失效和內部短路會存在起火風險。
這個思路與人體碰撞保護類似,任何法規(guī)在設計車的人體碰撞保護時,都不是要滿足給定的工況下不許受傷,而是再給定工況下產生一個可接受的受傷,盡量不要產生終身殘疾。因此,研究需要找出電池的碰撞損傷準則和容限,在起火前能承受的最大變形和最大沖擊。
拓撲優(yōu)化是結構優(yōu)化的一種,不同于車輛構件的尺寸優(yōu)化和形狀優(yōu)化,是對布局和節(jié)點聯接關系進行優(yōu)化,使結構的某種性能指標達到最優(yōu)化。
汽車廠在新車開發(fā)時,公司決策層會給出一個整車定義,包括車多大多重,涉及到成本控制,同時希望車達到什么性能。拓撲優(yōu)化能夠在給定設計空間,給定設計重量,給定設計性能的約束下,迅速得到一個布局和節(jié)點聯接基本判斷,為設計人員提供結構質量最輕、性能最優(yōu)的力學傳遞路徑方案。
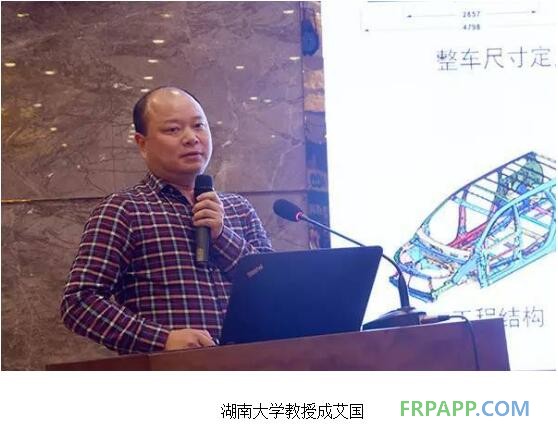
據湖南大學教授成艾國介紹,湖南大學已經用拓撲優(yōu)化的辦法對電動汽車的骨架進行優(yōu)化?;谕負鋬?yōu)化方法的輕量化策略相比常規(guī)輕量化方法可節(jié)約30天開發(fā)時間、多減重22.4kg,同時還可以不同程度的提升整車性能。
2.輕量化材料
目前輕量化材料主要有復合材料、鋁鎂合金、高強鋼和陶瓷材料。
鋼鐵材料是汽車生產的主要材質,在同等的強度條件下,如果采用高強度鋼就可以最大限度的減輕鋼板的厚度,達到減輕車身自重的目的。目前高強鋼主要應用在汽車的安全件、底盤和車身等方面。
鋁合金減重效果多于鋼鐵,汽車使用一公斤鋁合金等于2.25公斤的鋼鐵,鋁合金和鋼鐵材料相比,熱導率高、耐腐蝕性好、加工性能等優(yōu)良等優(yōu)點,但強度不如高強鋼。
工程塑料和復合材料是汽車輕量化的首選用材。
一般塑料的比重0.9-1.5%。在復合材料中,碳纖維材料具有密度低、強度高、耐腐蝕、耐高溫等特性被寄予厚望。發(fā)達國家已經把汽車用塑料量的多少作為衡量汽車設計和制造水平的一個重要標志。
汽車復合材料的發(fā)展結合了化工、機械制造和汽車復合材料設計等多學科的技術,它主要集中應用在汽車底盤、車身覆蓋件和次結構部件三個領域。許多企業(yè)的T700、T800和T1000碳纖維產品達到了一千噸以上的產能,并且將碳纖維材料在汽車上的應用作為主攻方向。
3.輕量化材料的成型技術
采用新工藝可大大減少零部件使用數量,實現輕量化目標。意大利APS技術有限公司總裁王嘉介紹,鋁型材的三維彎曲、鋼鋁焊接以及碳纖維零件的成型是目前面臨的全新工藝。

其中,碳纖維總成的方式已取得突破性進展,在蘭博基尼Sesto Elemento的項目中,將前圍、地板、后圍集成為一個整體式座艙,取代了傳統(tǒng)結構的48個零件,而是把零件分為4—6大片,成型之后直接粘接,工藝簡單,但減重效果突出。整備質量在加注燃料和其它液體前只有960 公斤。王嘉認為,2020年之后,熱塑成型碳纖維將越來越普及,鋼板被大量替代。
國內外汽車輕量化發(fā)展情況
在汽車輕量化方面,國內與國外企業(yè)相比,還存有不少差距。
德國在汽車輕量化方面處于領先低位,主要受益于工業(yè)結構。德國第一大工業(yè)是汽車,第二是機械制造,第三是化工,化工和機械制造比重相仿,這樣的工業(yè)結構使得他們在汽車輕量化應用方面,能夠從材料加工技術和整車方面能夠有很好的融合。
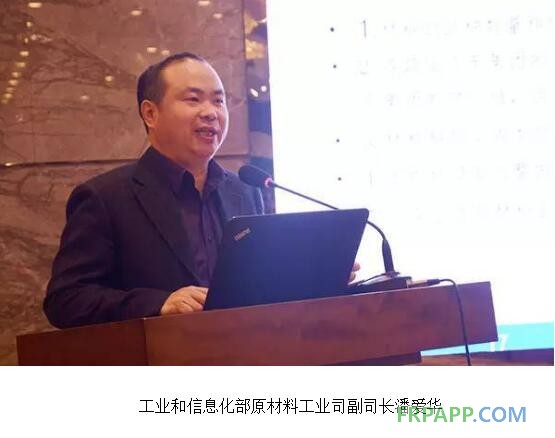
工業(yè)和信息化部原材料工業(yè)司副司長潘愛華指出,我國在輕量化研究上與發(fā)達國家存在5個方面的差距:
第一,材料行業(yè)本身。我國材料品種、數量、性能與國外還有很大差距。
第二,國內汽車行業(yè)。特別是合資品牌有自成體系的供應商鏈,國產材料企業(yè)進入非常困難,導致國內材料企業(yè)明顯滯后于汽車產業(yè)發(fā)展。
第三,材料和加工成本控制難度大。碳纖維這樣的復合材料,本身成本可能不是貴得多么離譜,但是由于加工效率低,導致了對汽車部件和汽車廠來說成本增加很大。
第四,標準缺失。我國還沒有完整的汽車塑料零部件技術和產品標準,包括技術方面的測試標準,還存在缺失。
第五,國內汽車企業(yè)和材料企業(yè)的融合不夠。
汽車輕量化帶來哪些變化?
一種生產模式的變化。奇瑞新能源汽車技術有限公司副總經理、研究院院長倪紹勇在分享時介紹,公司在做輕量化產品時,認為不是局限在做一個車,而是一個全新的架構,從根本上把傳統(tǒng)車的對于新能源來說不好的地方去除掉,充分體現電動化、新材料和新技術的特點。
奇瑞的S51車型是首個大批量生產的全鋁車身架構汽車產品,重量比傳統(tǒng)車減重30%到40%。采用共享的技術平臺,采用首款全鋁車身,改變了整體布置,采用技術創(chuàng)新,如斷面設計,3D的彎曲,激光焊接等,和傳統(tǒng)的車身制造、設計制造有很大不同。


一種供應模式的變化。汽車工程學會副秘書長張寧指出,在輕量化技術的逐漸發(fā)展中,原材料供應商變成了部件供應商。
例如碳纖維在汽車上的應用改變了傳統(tǒng)汽車的設計,開發(fā)流程、設計思想以及制造工藝,其根本原因在于碳纖維材料是可設計的,比如用長纖維還是短纖維等等。未來碳纖維應用于汽車沒有標準化的材料,整個車和零部件的開發(fā)過程就是材料開發(fā)過程。
一種組織結構的變化。單從車企來看,輕量化帶來了生產平臺和開發(fā)模式的調整,汽車廠不可能把所有的資源都變成自己的員工,一定要利用國際資源,利用廣泛社會資源來實現目的。
輕量化的問題很復雜,因此需要跨產業(yè)協同及產學研合作方面。目前這方面仍然存在不足。例如,現在理論上已經找到大幅提高碳纖維性能,使原有成本降低三分之一的方法,但是由于缺乏交叉學科人才,廠商與科研團隊之間溝通不暢,嚴重阻礙了輕量化進程。
如何推動汽車輕量化發(fā)展?
潘愛華在總結推動汽車輕量化發(fā)展時提到了四點:
第一,組織行業(yè)協會、企業(yè)和專家盡快建立中國汽車工業(yè)塑料材料的標準體系,并建立材料自身的材料論證體系,進行材料的性能檢測、應用驗證、技術穩(wěn)定性、安全可靠性評價等等。
第二,鼓勵產業(yè)鏈上下游合作組建產業(yè)聯盟,支持汽車工業(yè)與國內塑料行業(yè)之間深入交流,實現強強聯合,突破國產改性塑料進入汽車整車及關鍵零部件市場瓶頸,讓一部分性能穩(wěn)定、品質過硬的國產材料優(yōu)先進入汽車產業(yè)鏈。
第三,通過強基工程、智能制造工程、綠色制造工程等專項支持建立汽車材料應用評價公共服務平臺,以及汽車材料生產制造技術的產業(yè)化。
第四,推動電動汽車行業(yè)和化工行業(yè)的骨干企業(yè),聯合成立一個輕量化新材料的產業(yè)基金,聚集更多的社會力量來推動汽車輕量化。