“隨著碳纖維材料制造工藝進步,成本也在不斷下探,從應用的車型就可見一斑。之前都用在百萬級豪車上,現(xiàn)在許多國產(chǎn)30萬-40萬元車型上都有了碳纖維的身影,”第五屆進博會期間,復合材料綜合解決方案提供商HRC市場總監(jiān)陳文瑾在接受澎湃新聞記者采訪時表示,碳纖維材料正面對著越來越廣闊的市場空間。
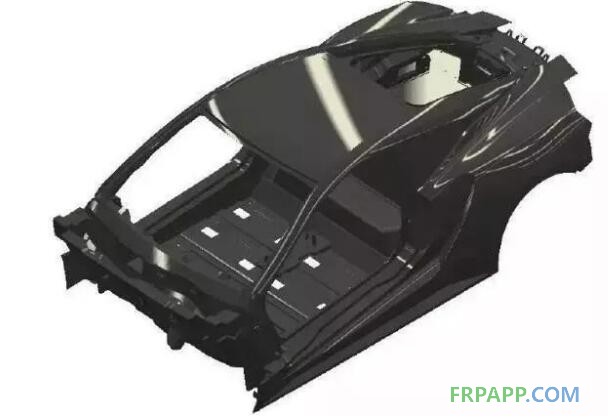
全碳纖維復合材料車身
HRC是一家專業(yè)從事輕量化高性能碳纖維零部件研發(fā)、工程設計和工業(yè)化量產(chǎn)的高科技型企業(yè)。今年是HRC第三次參加進博會,“HRC每一屆都在汽車展館中,這給我們提供了非常便捷的機會去了解來自世界各地的各大主機廠,從F1賽車到極地救援車,甚至是飛行汽車、水上汽車等等,每一年汽車館總是能帶來非常多的新理念。”陳文瑾說道。
碳纖維是一種含碳量在90%以上的高強度、高模量纖維的新型纖維材料。在現(xiàn)代工業(yè)體系中,碳纖維已經(jīng)不可或缺,大到飛機制造、小到羽毛球拍、魚竿等,都有碳纖維的身影。據(jù)海通證券研報,想要達到400公斤普通鋼的強度,需要使用優(yōu)質(zhì)鋼320公斤或鋁合金240公斤,而使用碳纖維則僅需160公斤,材料減重效果顯著。
在中國本土的碳纖維汽車零部件供應領域,HRC占據(jù)了最大的市場份額。
陳文瑾表示,在汽車領域,HRC的碳纖維零部件供應市場份額處于第一的位置。HRC目前與中國本土大部分主機廠都建立了合作,如吉利、比亞迪、廣汽、長城、長安、上汽等,不少項目已經(jīng)進入量產(chǎn)或即將開始量產(chǎn)。
她提到,在HRC最初進入中國市場時,中國主機廠基本都僅有材料部門,而并沒有專門的輕量化部門,隨著新能源車的崛起,輕量化這一領域逐漸受到了車企越來越多的重視。
由于鋰電池自重較大,相較于傳統(tǒng)燃油車,電動車重量大幅增加,在主流車型中,電池重量近500kg的車型不在少數(shù)。然而重量的增加限制了車輛的續(xù)航里程,車企就需要通過減輕其他零部件的重量來降低車身自重,進而增加續(xù)航里程、提升車輛駕控性能,碳纖維這種強度高、密度低的復合材料也就成為了車企的不二選擇。
據(jù)介紹,在中國市場,HRC已經(jīng)覆蓋了復合材料零部件開發(fā)及成型的各個環(huán)節(jié),從材料選擇、工藝推薦到最終的批量生產(chǎn),形成一個具有高技術壁壘的服務閉環(huán)。
陳文瑾提到,隨著碳纖維制造工藝的進步、成本的下降,其在汽車行業(yè)的應用范圍不斷擴大,已從百萬元以上的車型拓展到30萬-40萬元車型上,同時也在從車輛外部走進車輛內(nèi)部,“例如不少車企已經(jīng)開始在A柱、B柱等汽車結構件上使用碳纖維材料,這對于HRC來說,都是巨大的潛在增長空間。”
值得注意的是,碳纖維材料的應用,也在助力汽車行業(yè)實現(xiàn)使用過程中的碳減排。
陳文瑾介紹,汽車整車重量降低10%,燃油效率可提高6-8%。對傳統(tǒng)車而言,輕量化可直接減少化石燃料,減少污染排放。此外,在某種程度上,輕量化意味著可持續(xù)性,因為在制造過程中使用的初級資源更少,實際使用時的能耗也更低。