1 ·引言
高壓玻璃鋼管道固化成型工藝自傳統(tǒng)固化工藝改進(jìn)而來(lái),目前已經(jīng)在玻璃鋼管道生產(chǎn)中得到了廣泛應(yīng)用[1]。與傳統(tǒng)固化工藝相比,該工藝由于采用內(nèi)部加熱方式,因此更加適合于高壓管道的制造[2,3]。玻璃鋼管道主要靠纖維承壓,采用樹(shù)脂充當(dāng)粘合劑,因此對(duì)于高壓殼體的生產(chǎn),要嚴(yán)格控制樹(shù)脂的含量[4]。如圖1 所示,根據(jù)樹(shù)脂的黏度特性,控制樹(shù)脂含量即為控制管道固化過(guò)程中內(nèi)部溫度[5],根據(jù)本文所選用樹(shù)脂的黏度特性,期望的溫度范圍為70 ~ 90℃。
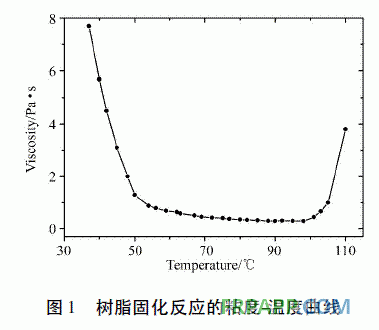
影響正在纏繞的玻璃鋼管道外表面溫度的因素眾多,其中芯模的加溫歷程對(duì)其影響最大。本文利用有限元軟件ANSYS 和APDL 語(yǔ)言開(kāi)發(fā)了數(shù)值模擬程序,對(duì)采用傳統(tǒng)恒溫加熱的熱芯纏繞工藝?yán)p繞過(guò)程( 以下簡(jiǎn)稱纏繞過(guò)程) 進(jìn)行了數(shù)值模擬,分析了外表面溫度受加溫歷程影響規(guī)律,繼而優(yōu)化纏繞過(guò)程的加溫歷程使復(fù)合材料外表面溫度在期望的范圍內(nèi)。
2· 數(shù)值模擬
以纏繞20 層、厚度為6. 6mm、纖維體積含量為60%的DN65 高壓玻璃鋼管道為例,按照60s /層的纏繞速率進(jìn)行纏繞。對(duì)該固化成型工藝進(jìn)行數(shù)值模擬仿真及分析。材料的熱學(xué)性質(zhì)和固化動(dòng)力學(xué)參數(shù)分別如表1、表2 所示。

玻璃鋼管道含膠量的控制實(shí)質(zhì)上就是纏繞過(guò)程中外表面溫度的控制,而纏繞過(guò)程的加溫歷程是影響外表面溫度的重要因素。因此本文根據(jù)傳統(tǒng)的恒溫加熱對(duì)纏繞過(guò)程進(jìn)行數(shù)值模擬,分析了纏繞過(guò)程中溫度、放熱反應(yīng)強(qiáng)度的分布和外表面溫度的變化規(guī)律。傳統(tǒng)的恒溫加熱在纏繞第1 層時(shí)芯模以65℃ /min 的升溫速率從室溫35℃升高到100℃,在纏繞接下來(lái)的19 層時(shí)芯模溫度恒定在100℃,仿真所得第1 層、2 層、5 層、7 層、10 層、15 層和20 層外表面中心節(jié)點(diǎn)的溫度隨時(shí)間變化曲線如圖2 所示。

3 ·纏繞過(guò)程加溫歷程的優(yōu)化
為了清楚地分析纏繞過(guò)程中管道外表面溫度變化規(guī)律,本文將纏繞下一層時(shí),殼體前一層外表面中心節(jié)點(diǎn)的溫度( 以下簡(jiǎn)稱纏繞過(guò)程中管道的外表面溫度) 列為表3。

由表3 可見(jiàn),第2、3 層外表面的溫度超出了工藝要求的最高溫度90℃。隨著纏繞的繼續(xù),外表面的溫度逐漸降低,第11 層外表面溫度已經(jīng)低于工藝要求的最低溫度70℃,此時(shí)外表面的黏度增大,不利于樹(shù)脂更好地浸漬纖維,也不利于多余樹(shù)脂的排出。由此可見(jiàn),實(shí)際生產(chǎn)中所使用的纏繞過(guò)程中的加溫歷程是不合理的?;谏鲜鰡?wèn)題,本文通過(guò)優(yōu)化纏繞過(guò)程的加溫歷程( 分為a、b、c 三個(gè)階段) 來(lái)控制管道的外表面溫度,使其始終維持在工藝要求的溫度范圍內(nèi)。優(yōu)化后和優(yōu)化前的溫度對(duì)比如圖3 所示,由圖可見(jiàn)優(yōu)化后的溫度始終控制在期望的范圍內(nèi)。

4 ·結(jié)論
本文利用有限元軟件ANSYS 和APDL 語(yǔ)言開(kāi)發(fā)了數(shù)值模擬程序,對(duì)高壓玻璃鋼管道的固化成型過(guò)程進(jìn)行了數(shù)值模擬,分析了纏繞過(guò)程中管道外表面溫度的變化規(guī)律,對(duì)采用傳統(tǒng)恒溫加熱的纏繞過(guò)程進(jìn)行了優(yōu)化,保證了在纏繞過(guò)程中管道外表面溫度始終在工藝要求的范圍內(nèi),從而提高高壓玻璃鋼管道的耐壓能力。