高推重比、低耗、低污染物排放是航空發(fā)動機未來發(fā)展的重要方向。研發(fā)高性能材料替代傳統(tǒng)金屬材料,實現(xiàn)結構減重是推動航空發(fā)動機進步的關鍵途徑。樹脂基復合材料具有質(zhì)輕高強、結構可設計性好、抗疲勞性能好、阻尼減振性能優(yōu)異、易于一體化整體成型的優(yōu)點,已成為飛機發(fā)動機冷端部件理想的結構材料,其用量多少也是評價航空發(fā)動機先進性的重要標志。隨著復合材料設計水平提升、原材料性能提高、制造工藝進步、可靠性驗證方法完善,樹脂基復合材料在民用渦扇發(fā)動機上應用走過了一條由少到多、由次承力到主承力、由局部到整體的發(fā)展道路。目前樹脂基復合材料在國外多型渦扇發(fā)動機風扇葉片、風扇機匣等重要部件上實現(xiàn)了較為成熟的應用。借鑒國外航空發(fā)動機樹脂基復合材料的研發(fā)應用經(jīng)驗,立足自我創(chuàng)新,加快推進樹脂基復合材料在我國民用航空發(fā)動機上應用,既帶來了機遇也提出了巨大的挑戰(zhàn)。

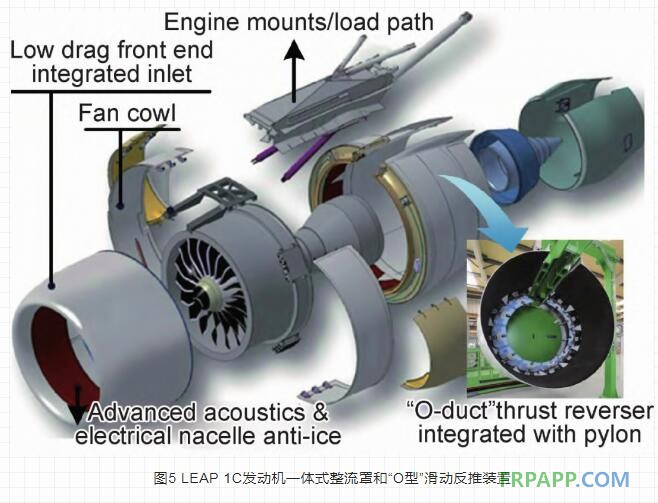

一、樹脂基復合材料在國外民用航空發(fā)動機的應用狀況
近些年美國通用電氣公司、美國普拉特·惠特尼公司、英國羅爾斯·羅伊斯公司等在樹脂基復合材料發(fā)動機部件應用方面取得了較大進展。以普·惠公司為例,1970年首先在JT9D發(fā)動機上使用玻璃纖維/環(huán)氧樹脂復合材料制備了風扇整流錐。為了進一步減重,1981年采用芳綸纖維/環(huán)氧樹脂復合材料制備了JT9D-TR4發(fā)動機整流錐。之后樹脂基復合材料被大量應用于普·惠發(fā)動機上,如PW4084發(fā)動機樹脂傳遞模塑工藝制備的碳纖維/環(huán)氧樹脂風扇葉片墊塊、PW4168發(fā)動機雙馬樹脂復合材料整流罩和碳纖維/環(huán)氧樹脂復合材料反推力裝置等短艙部件。圖1列出了目前國外民用渦扇發(fā)動機樹脂基復合材料應用部位、材料體系及制備工藝。圖中1~12依次為渦扇發(fā)動機電控單元匣、進氣道消聲襯板、風扇葉片、進氣整流錐、進氣整流罩、發(fā)動機檢視門、反推力裝置、壓氣機整流罩、外涵道、出口導流葉片、風扇機匣、發(fā)動機短艙等部件。以下將對國外民用航空發(fā)動機典型樹脂基復合材料部件應用發(fā)展狀況進行詳細分析。
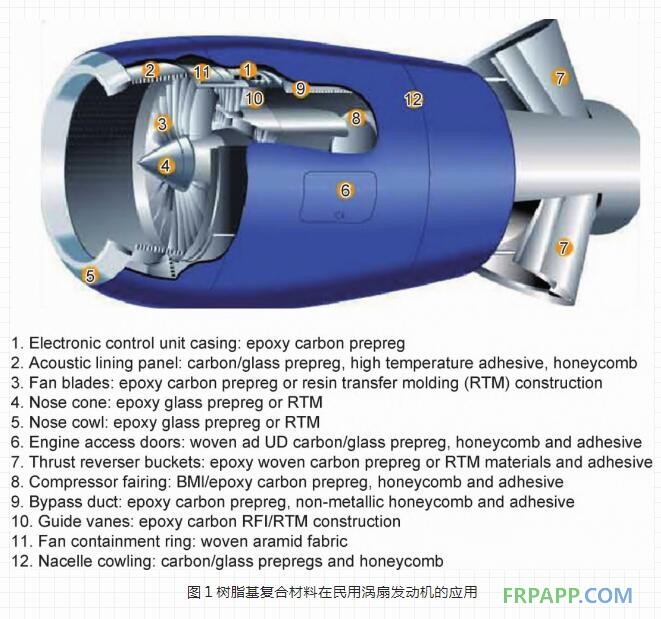
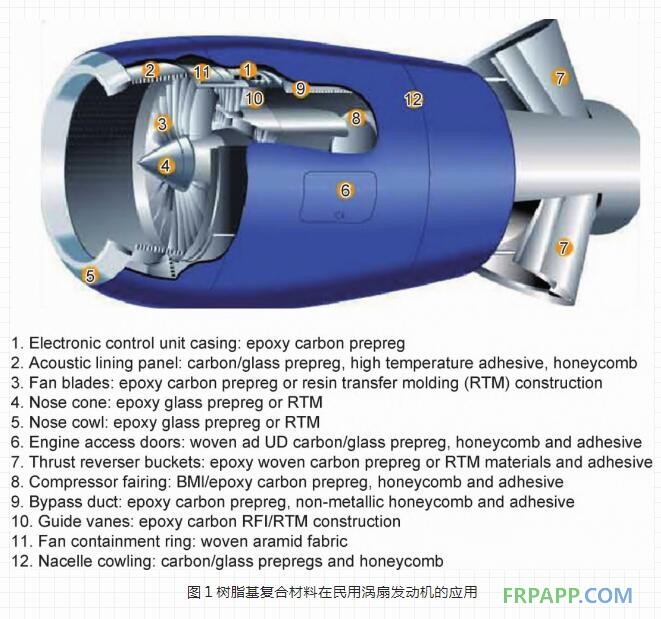
1.1 風 扇 葉 片
20世紀70年代,羅·羅公司最早嘗試將碳纖維樹脂基復合材料應用于RB211發(fā)動機風扇葉片。但由于所使用復合材料基體韌性較低,最終未能通過風扇葉片鳥撞測試,導致該型發(fā)動機沿用了傳統(tǒng)鈦合金風扇葉片。
隨著低質(zhì)量、高進氣效率、大涵道比航空發(fā)動機的研發(fā)及樹脂基復合材料性能的提高,20世紀90年代通用電氣公司選取美國赫氏公司HexPly 8551-7韌性環(huán)氧樹脂為基體,IM7碳纖維為增強纖維,采用單向預浸料模壓工藝制備GE90發(fā)動機進氣風扇葉片。葉片表面涂覆聚氨酯防腐涂層提高葉片抗腐蝕性能。葉片前緣使用美國3M公司AF191膠黏劑粘接鈦合金薄片增強葉片抗沖擊性能。葉片根部具有自潤滑特氟龍耐磨層(圖2(a))。此后通用電氣公司GEnx和GE9X型發(fā)動機均采用樹脂基復合材料風扇葉片。

在適用于單通道客機的中小推力發(fā)動機方面,傳統(tǒng)CFM56系列發(fā)動機采用鈦合金風扇葉片及合金鋼金屬機匣。為進一步減輕發(fā)動機質(zhì)量,降低燃油消耗,美國通用電氣和法國賽風集團旗下斯奈克瑪公司合資成立的CFM國際公司開發(fā)了LEAP系列發(fā)動機。LEAP系列發(fā)動機風扇葉片采用3D整體編織技術制備了具有三維交織結構且近似零尺寸誤差的纖維預成型體(圖2(b))。通過樹脂傳遞模塑工藝灌注樹脂實現(xiàn)纖維浸潤和樹脂固化(圖3)。其中纖維三維編織結構可有效提高葉片抗沖擊性能。
2020年1月上旬,羅·羅公司在英國布里斯托開始了名為“超級風扇”的發(fā)動機原型機制造。該發(fā)動機采用全樹脂基復合材料風扇葉片和機匣。風扇葉片由碳纖維/韌性樹脂預浸料鋪貼固化而成。葉片前緣采用與GE90風扇葉片相似的鈦合金包邊,起抗腐蝕和異物沖擊作用。羅·羅公司預計該型發(fā)動機裝機服役后,可實現(xiàn)飛機整體減重700kg,相比第一代遄達系列發(fā)動機更為省油,降低至少25%的二氧化碳排放。
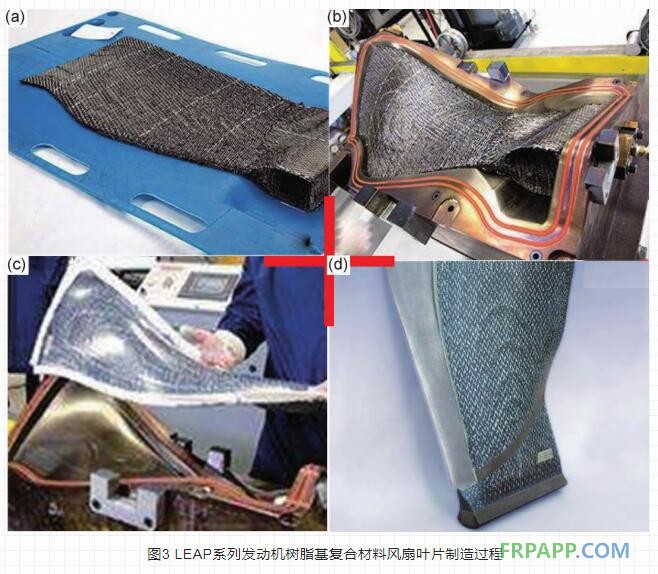
1.2 風 扇 機 匣
發(fā)動機運轉過程中葉片因遭受撞擊或疲勞斷裂時,風扇機匣對脫落葉片起包容作用,避免其對飛機其他部分造成損害。因而風扇機匣是維系飛機服役安全可靠的重要部件。
早期渦扇發(fā)動機風扇葉片多為鈦合金材質(zhì),一旦脫落對風扇機匣的沖擊能量較大。風扇機匣多采用鋁合金、鈦合金或高強度合金鋼制造,以增加結構厚度提高包容效果,稱為硬包容。之后研發(fā)出以環(huán)形金屬機匣殼體為內(nèi)襯,外部依次纏繞若干圈芳綸纖維編織條帶為保護層的復合結構機匣,依靠芳綸纖維層易于發(fā)生大變形吸能的特點捕獲碎片,故而稱為軟包容。
由于發(fā)動機風扇涵道比日趨增大,風扇部分在發(fā)動機總重中占比變大,高性能輕量化的要求越發(fā)迫切。伴隨著GE90系列發(fā)動機復合材料風扇葉片的成熟使用,在后續(xù)GEnx型發(fā)動機上GE公司研發(fā)了全復合材料風扇機匣。該機匣采用自動化二維三軸編織技術將日本東麗公司TORAYC T700碳纖維按0°及±60°三個方向編織成厚度為7.62mm纖維預成型體。利用樹脂傳遞模塑工藝灌注CYCOM PR520環(huán)氧樹脂比利時索爾維集團旗下氰特公司產(chǎn)品固化成型。法國賽風集團旗下斯奈克瑪公司也采用了增強纖維3D編織技術及樹脂傳遞模塑工藝制備了LEAP系列發(fā)動機復合材料風扇機匣。
1.3 聲 襯
進氣風扇噪聲已成為現(xiàn)代大涵道比航空發(fā)動機噪聲的主要來源。在進氣道內(nèi)鋪設聲襯是航空發(fā)動機消聲降噪的重要方式之一。聲襯所具有的穿孔板蜂窩結構可視為數(shù)個并聯(lián)的亥姆霍茲共振結構。當其共振頻率與噪聲頻率匹配時起到消聲效果。傳統(tǒng)單自由度聲襯噪聲吸收頻帶較窄,多自由度聲襯雖能拓寬吸聲頻帶,但也存在加工工藝復雜、尺寸較大、結構增重較多的問題。
基于以上問題,赫氏公司開發(fā)了商品名為Acousti-Cap的隔帽內(nèi)嵌式蜂窩,如圖4所示。由表面穿孔柔性材料(如聚醚醚酮,PEEK)折疊成隔帽形狀嵌入蜂窩腔中膠粘定位,從而起到雙自由度聲襯中聲學隔膜的作用。蜂窩聲阻抗特性可以由以下幾個因素調(diào)節(jié):(a)蜂窩腔中隔帽數(shù)量;(b)蜂窩腔中隔帽位置;(c)不同種類聲阻抗特性隔帽。相比傳統(tǒng)多自由度聲襯,采用該種蜂窩制備聲襯厚度較薄、所需安裝空間小、聲襯整體結構強度較高。目前此蜂窩已用于通用電氣、羅·羅、CFM國際等公司生產(chǎn)的多型航空發(fā)動機,不僅減輕了質(zhì)量而且實現(xiàn)了多達30%的噪聲衰減。

1.4 襯 套
傳統(tǒng)樹脂基復合材料基體耐溫性能較低,通常應用于航空發(fā)動機冷端結構及外部覆蓋件。以聚酰亞胺樹脂為代表的耐高溫樹脂基體研發(fā)使樹脂基復合材料用于航空發(fā)動機近熱端部件成為可能。聚酰亞胺襯套是樹脂基復合材料在壓氣機等耐溫要求較高部位的典型應用之一。襯套用聚酰亞胺復合材料不僅滿足長期工作溫度280℃左右,短時經(jīng)受400℃以上的耐溫要求,同時具有良好的熱尺寸穩(wěn)定性、自潤滑性、低摩擦系數(shù)、優(yōu)異的耐磨損性能和力學性能。美國杜邦公司(USA,DuPont Company)開發(fā)了Vespel系列聚酰亞胺復合材料,其中包括石墨填充聚酰亞胺復合材料(如Vespel SP-21,SP-22等)及碳纖維織物增強聚酰亞胺復合材料(如Vespel CP- 8000,CP-0664等)。該系列聚酰亞胺復合材料已應用于羅·羅公司BR710型、普·惠公司PW6000系列等多型航空發(fā)動機壓氣機可調(diào)靜子葉片襯套。
二、樹脂基復合材料在民用航空發(fā)動機的應用優(yōu)勢
2.1 有利于航空發(fā)動機結構優(yōu)化
現(xiàn)代渦扇發(fā)動機風扇葉片運轉時可能承受約100t離心載荷。離心載荷隨風扇直徑、旋轉速度和葉片質(zhì)量的增加而增大。使用樹脂基復合材料降低風扇葉片質(zhì)量可以增加風扇葉片尺寸及轉速的設計裕度?;趶秃喜牧蟽?yōu)異的可設計性,復合材料風扇葉片具有S形后掠寬弦的高效氣動外形,因而使用較少的葉片數(shù)量仍有較高的進氣效率。同時相比鈦合金中空結構風扇葉片,可實現(xiàn)10%~15%的減重。
隨著復合材料風扇葉片設計水平的進步和材料性能的提升,經(jīng)過GE90,GEnx,GE9X數(shù)個代次發(fā)展,GE公司發(fā)動機復合材料風扇葉片呈現(xiàn)數(shù)目降低、厚度變薄、性能更強的趨勢。GE90,GEnx,GE9X三型發(fā)動機分別有22,18,16片復合材料風扇葉片。其中最新型GE9X發(fā)動機風扇葉片采用剛度更高的碳纖維作為增強體,可使風扇葉片長度更長、厚度更薄,進氣效率更高。此外該葉片使用抗沖擊性能更為優(yōu)異的合金鋼替代了GE90、GEnx發(fā)動機風扇葉片的鈦合金前緣包邊,后緣為特殊結構的玻璃纖維復合材料,通過葉片前后緣局部加強措施風扇葉片抗沖擊性能進一步提升,可使葉片整體厚度更薄。因此盡管GE9X風扇直徑達3.4m,但發(fā)動機風扇更輕、轉速更快、氣動效率更高,綜合性能更為優(yōu)異。復合材料風扇葉片的應用促使碳纖維織物/環(huán)氧樹脂復合材料包容機匣的產(chǎn)生。全復合材料包容機匣不僅質(zhì)量輕,而且兼具較高的結構剛度和較好的彈性變形,可實現(xiàn)對復合材料葉片的良好包容。
材料和結構同時成型是樹脂基復合材料區(qū)別于金屬材料的特點之一。這為航空發(fā)動機大型復雜部件的整體化設計、一體化制造提供了可能。美國奈賽公司摒棄了傳統(tǒng)的分離式子系統(tǒng)設計理念,在中國商飛公司C919大型客機裝備的LEAP-1C發(fā)動機上開發(fā)了集成式推進系統(tǒng)。其中包括一體式復合材料進氣整流罩和整體復合材料“O型”滑動反推裝置(圖5)。此外變傳統(tǒng)發(fā)動機進氣道拼接式聲襯為環(huán)形無拼接式聲襯也是復合材料整體成型工藝應用的典型案例。
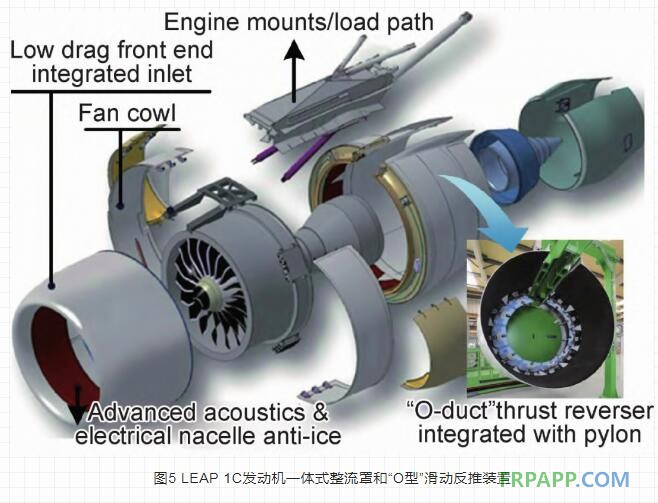
2.2 有利于提高航空發(fā)動機經(jīng)濟性
減輕發(fā)動機質(zhì)量是航空發(fā)動機提高燃油效率和推重比的重要途徑。樹脂基復合材料質(zhì)輕高強,應用于風扇葉片、包容機匣等部件有效降低了發(fā)動機結構質(zhì)量。例如CFM56-7B發(fā)動機24片鈦合金風扇葉片總質(zhì)量118kg,而LEAP系列發(fā)動機18片復合材料風扇葉片總質(zhì)量僅76kg。相比同尺寸金屬材質(zhì)葉片和機匣,使用樹脂基復合材料制備可實現(xiàn)整體減重455kg。
采用復合材料共固化、共膠接等整體成型技術制備大型復雜結構件,一方面可以通過結構優(yōu)化提升發(fā)動機性能,另一方面可減少子部件數(shù)目,降低因部件裝配連接引起結構增重及性能損失。與傳統(tǒng)發(fā)動機多塊式拼接鋁合金唇口及進氣道相比,LEAP-1C發(fā)動機一體式無縫復合材料進氣整流罩,可避免流場不連續(xù)性造成的進氣效率降低。整體化復合材料“O型”滑動反推裝置替代典型兩片式“D型”門設計,不僅提高了反推效率,而且實現(xiàn)了原有笨重液壓驅動系統(tǒng)到先進電控驅動系統(tǒng)的轉變,解決了“D型”門聯(lián)鎖機構需持續(xù)性維護的問題??偟膩砜矗墒酵七M系統(tǒng)增強了發(fā)動機的空氣動力學性能,通過結構優(yōu)化整合減少發(fā)動機質(zhì)量、降低燃油消耗、可靠性更高、更易于維護,這些都將有效提高發(fā)動機的經(jīng)濟性,降低飛機運營成本。
從制造及檢測的機械化自動化角度看,現(xiàn)階段機械自動化預浸料裁剪、激光定位鋪覆及纖維三維預成型體編織技術已得到較為成熟的應用。近期在羅·羅公司“超級風扇”發(fā)動機原型機制造計劃中,復合材料風扇葉片和機匣分別采用了自動鋪絲(圖6(a))及自動鋪帶工藝(圖6(b))制造。而三維激光測量技術(圖6(c))和水下超聲探傷技術(圖6(d))也應用于風扇葉片葉形、尺寸測量和內(nèi)部缺陷探測等檢驗過程中。機械自動化水平的提高,不僅提升了工作效率,保證了復合材料部件制造檢測過程的標準化、準確化,同時降低了廢品率和人工費用,有利于縮減航空發(fā)動機制造成本。

復合材料優(yōu)異的抗疲勞耐久性能可顯著降低服役過程中部件的修理維護成本。數(shù)據(jù)顯示已裝機使用的GE90復合材料風扇葉片在總計750萬個飛行小時里無須專門檢查和現(xiàn)場特別維護。盡管在服役期間經(jīng)歷了多達100次的鳥撞沖擊,但僅有三片復合材料葉片需徹底更換,顯示出良好的可靠性和經(jīng)濟性。此外復合材料風扇葉片葉根處具有自潤滑特氟龍耐磨層,當葉片裝入燕尾槽后無需加入潤滑劑,免去了定期潤滑維護成本。
2.3 有利于提高航空發(fā)動機環(huán)保性
在當今世界環(huán)保要求日益提高的要求下,航空發(fā)動機尾氣排放及噪聲級別已成為各航空發(fā)動機制造商關注的重點。樹脂基復合材料可有效減輕發(fā)動機結構質(zhì)量、減少燃油消耗、降低航空發(fā)動機尾氣排放量,有利于提高其環(huán)保性。相比CFM56系列發(fā)動機,應用大量復合材料部件的LEAP系列發(fā)動機燃油消耗及二氧化碳排放量減少了15%,氮氧化物排放量減少了60%。
發(fā)動機噪聲是飛機噪聲的主要來源。隨著渦扇發(fā)動機涵道比增大,進氣風扇噪聲在發(fā)動機噪聲中占比逐漸增加。傳統(tǒng)進氣道消聲板為拼接分片式設計,拼接造成進氣道壁面聲阻抗不連續(xù),削弱了消聲效果。如圖7所示,歐洲空中客車公司早期A320飛機發(fā)動機進氣道聲襯拼縫為3片15cm,之后A340 600飛機發(fā)動機為2片7.5cm寬。采用樹脂基復合材料整體成型工藝后,A380飛機發(fā)動機為環(huán)形無拼接聲襯。




國際民用航空組織于1972年首次在國際民用航空公約附件16第二章對飛行器噪聲控制提出要求,稱之為第二章噪聲控制標準。在1977年實施第三章噪聲控制標準,該標準中對不同起飛質(zhì)量飛行器飛越、橫側、進近及上述三者累積噪聲均提出了要求。之后ICAO分別提出了要求更為嚴格的第四章和第十四章噪聲控制標準,其累積噪聲比第三章噪聲分別低了10dB和17dB。而美國聯(lián)邦航空管理局依據(jù)ICAO各章噪聲標準分別定義了第二、三、四、五階段噪聲控制標準(Stage2/3/4/5)(如圖8所示)。

受益于復合材料進氣道無拼接聲襯及進氣風扇葉片高效率低噪聲設計,GE9X發(fā)動機運轉噪聲低于第五階段噪聲要求且有8dB裕量。此外歐洲航空安全局對安裝LEAP-1A發(fā)動機的空客A321neo飛機開展了飛行噪聲測試。數(shù)據(jù)顯示A321neo飛機飛越、橫側及進近噪聲分別為83.3,88.3dB和94.7dB,均低于裝配CFM56發(fā)動機的空客A321飛機,滿足第四階段噪聲控制要求。
三、樹脂基復合材料民用航空發(fā)動機應用的新趨勢
3.1 微納材料混雜技術
航空發(fā)動機短艙、風扇葉片等在檢修維護及服役過程中易受到不同速度的異物沖擊而產(chǎn)生內(nèi)部層間分層乃至貫穿性失效破壞。目前通常采用纖維增強體3D編織或縫合技術,在復合材料厚度方向引入編織或縫合纖維提高復合材料層間斷裂韌性和抗沖擊性能。然而3D纖維增強結構較高的制造成本,加工過程中纖維損傷引起面內(nèi)性能下降也是制約其廣泛應用的重要問題。相比于傳統(tǒng)金屬材料,復合材料導電性較弱,發(fā)動機部件在經(jīng)受閃電沖擊時易產(chǎn)生結構破壞危及飛行安全?;谝陨蟽牲c,通過多尺度微納顆粒混雜技術提高樹脂基復合材料層間斷裂韌性及導電性能,實現(xiàn)結構功能一體化部件研發(fā)應用引起了眾多學者的關注。
目前使用較多的納米填料有碳納米管(CNT)、石墨烯、氧化石墨、炭黑、納米纖維等。Bhanuprakash等在環(huán)氧樹脂基體中加入改性氧化石墨納米填料后,玻璃纖維/環(huán)氧復合材料Ⅰ,Ⅱ型層間斷裂韌性均有大幅度提高。這與該填料加入碳纖維織物環(huán)氧復合材料所得結論一致。Srivastava等將3%(質(zhì)量分數(shù),下同)CNT、石墨烯和炭黑顆粒分別加入碳纖維環(huán)氧樹脂復合材料中,結果顯示加入石墨烯和CNT的試樣分別在Ⅰ,Ⅱ型層間斷裂韌性有最大值。盡管將納米填料直接混入樹脂基體的方法簡單方便,但納米填料添加量較高時樹脂黏度增大,造成工藝實施困難,納米填料團聚引起樹脂浸漬不良易在制件內(nèi)部產(chǎn)生缺陷。因此研究者通過在層間引入納米纖維布或具有高納米填料含量的樹脂膜或粉等方式改善復合材料層間斷裂韌性。Shin等將最高9%CNT混入樹脂,以含納米管樹脂膜的形式引入單向和織物碳纖維層板中。結果表明兩種層板的Ⅱ型層間斷裂韌性均先上升后下降,在CNT質(zhì)量分數(shù)為3%時有最大值。作者認為CNT橋連效應對裂紋擴展起阻滯作用,提高了Ⅱ型層間斷裂韌性。Abidin等通過在碳纖維復合材料鋪層間添加含碳納米管的樹脂粉末,復合材料Ⅰ型層間斷裂韌性有較大幅度改善。Ou等在碳纖維/環(huán)氧樹脂復合材料界面間插入低密度碳納米管紗,其Ⅰ型層間斷裂韌性提高了60%。
此外,聚砜、聚苯乙烯、尼龍66、聚丙烯腈、聚乙烯醇縮丁醛、聚氨酯等聚合物材料可通過靜電紡絲制備成納米纖維布插入復合材料層間改善纖維增強樹脂基復合材料Ⅰ,Ⅱ型層間斷裂韌性。研究發(fā)現(xiàn)聚苯乙烯納米纖維布不僅能提高復合材料層板層間斷裂韌性同時對層板面內(nèi)性能也有增強作用。而層間引入尼龍66導致復合材料層板厚略有增加,拉伸強度稍有下降。聚砜納米纖維布在復合材料層板固化升溫后與環(huán)氧樹脂混溶,冷卻后以微球形式發(fā)生相分離,其與環(huán)氧樹脂基體粘接較弱導致復合材料層板彎曲強度和模量下降。為解決以上問題,采用聚砜/碳納米管、聚丙烯腈/氧化鋁、聚丙烯腈/碳納米管]等不同納米填料混合使用可避免單一納米纖維布對面內(nèi)性能的負面作用。Handschuh等在復合材料葉片前緣預浸料鋪層中插入熱塑性聚氨酯納米布以改善復合材料韌性提高葉片抗沖擊性能。結果表明經(jīng)增韌處理后,復合材料葉片未發(fā)生目視可見的分層等表觀破壞,而未經(jīng)增韌處理的葉片分層及斷裂破壞嚴重。
采用導電率較好的納米填料“生長”或覆蓋于纖維表面不僅能夠提高復合材料層間斷裂韌性,同時可有效改善復合材料結構的導電性能。Bhanuprakash等將氧化石墨烯及改性氧化石墨烯分別覆蓋于碳纖維表面,其制備的環(huán)氧樹脂復合材料Ⅰ型層間斷裂韌性及導電性均有不同程度提高。Pozegic等研究表明通過在碳纖維表面生長CNT,碳纖維環(huán)氧樹脂復合材料在面內(nèi)方向導電率提高了330%。因層間厚度方向上形成了導電滲流通道,厚度方向導電率提高更為明顯(達550%),這與文獻中復合材料厚度方向導電性能顯著提升的結果一致。Duongthipthewa等在生長有碳納米管的碳纖維表面施加石墨烯后,碳纖維/環(huán)氧樹脂復合材料面內(nèi)和厚度方向導電率分別提高了300%和190%,沖擊性能提高了71%。針對不同樹脂基體,Russello等采用表面生長有碳納米管的碳纖維織物分別制備了熱固性環(huán)氧樹脂和熱塑性聚丙烯樹脂薄層復合材料,結果顯示后者導電性能提高幅度更大。
3.2 3D打印技術
3D打印,又稱增材制造,是目前材料制造工藝發(fā)展的熱點方向之一。傳統(tǒng)制造方法通過車銑刨磨等“減法”工藝過程實現(xiàn)由原材料坯體到部件的制備。3D打印則采用逐層累積的“加法”工藝過程自下而上制造出部件。依照增材制材料狀態(tài)及成型方式可分為光固化立體成形、熔融沉積成型、激光選區(qū)燒結、分層實體制造等。相比較傳統(tǒng)制造工藝,增材制造可實現(xiàn)小批量定制化復雜部件的快速精確成形、減少原材料浪費、節(jié)約模具和人工成本、簡化制造工序縮短制造周期。
目前3D打印技術在航空航天領域應用呈逐年上升趨勢。3D打印技術制備的航空發(fā)動機部件主要有燃油噴嘴、渦輪葉片等金屬部件。近些年在3D打印樹脂及其復合材料方向也開展了初步的研究工作。美國國家航空航天局蘭利研究中心采用光固化立體成形技術制造了純樹脂材質(zhì)變厚度聲襯模型件,并使用掠流阻抗管驗證了變厚度聲襯的消聲特性(圖9(a))。格倫研究中心選取Stratasys公司Ultem9085樹脂體系,采用熔融沉積法制備了聲襯和穿孔發(fā)動機檢視門(圖9(b),(c))。風洞實驗表明該工藝制造的聲襯與傳統(tǒng)蜂窩芯/穿孔面板聲襯相比具有相似的吸聲性能。為提高制件力學性能該中心將10%短切AS4碳纖維加入Ultem1000樹脂體系,使用熔融沉積法制備了壓氣機入口導流葉片(圖9(d))。研究發(fā)現(xiàn)相比未添加短切碳纖維樹脂體系,添加后拉伸強度和模量分別提高了23%和38%,但制件孔隙率達25%,脆性較大。這是由于碳纖維填充Ultem1000樹脂體系后,在420℃時熔體黏度才能滿足工藝要求。高溫會使樹脂體系中低分子量水汽等揮發(fā)性組分及擠出過程中卷裹的氣體膨脹,從而導致出口導向葉片孔隙率較高。作者認為通過控制Ultem1000樹脂體系分子量分布,使其在較低溫度下具有合適的工藝操作,黏度可在一定程度上降低制件孔隙率。

此外Impossible Objects公司所研發(fā)的碳纖維/聚醚醚酮樹脂體系可耐250℃高溫。其制件性能為傳統(tǒng)鋁合金的三分之二,但質(zhì)量僅為鋁合金的1/2,可用于航空機部件3D打印工藝。
3.3 超材料技術
超材料這一概念首先由電磁學領域學者所提出,其定義為周期性或非周期性人造微結構單元排列而成的復合材料。這類材料可呈現(xiàn)天然材料所不具備的超常物理特性。近些年超材料在聲學領域研究得到了越來越多的重視,通過特殊細觀結構設計可實現(xiàn)噪聲捕獲和衰減,這為未來航空發(fā)動機聲襯設計提供了新的思路。
當噪聲頻率較低時,穿孔板蜂窩式聲襯需增加結構厚度滿足消聲需求,而航空發(fā)動機內(nèi)部有限的聲襯安裝空間制約了傳統(tǒng)聲襯在航空發(fā)動機低頻噪聲消減方面的性能。超材料獨特的結構可設計性有助于解決這一矛盾。Li等和Chen等分別設計了兩種空間螺旋結構,配合微穿孔面板,可以有效降低結構厚度,擴大低頻噪聲吸收范圍(圖10(a),(b))。Yang等通過彎曲、回折式聲腔形式實現(xiàn)了結構厚度、吸收頻域和低頻吸收能力三者之間的平衡(圖10(c))。Tang等通過在傳統(tǒng)蜂窩式聲襯結構中引入斜向微孔隔板的超材料形式,滿足了隨機入射聲波寬頻高效吸收的要求(圖10(d))。Jiang等提出了由不同深度亥姆霍茲共振器與近似零折射率聲學超材料構成的單向超表面概念。當聲波進入該結構后即被“捕獲”,并在連續(xù)反射與吸收中達到能量彌散(圖10(e))。將單向超表面置于航空發(fā)動機聲襯與短艙內(nèi)表面之間,可以將噪聲在空間上限制于聲襯作用區(qū)域,進而起到協(xié)同作用,促進噪聲吸收。復雜且精細的結構是超材料發(fā)揮其性能的關鍵因素,而傳統(tǒng)材料加工工藝難于加工制造。目前已有研究者采用3D打印凱夫拉纖維/熱塑性樹脂制備了與文獻相似的波紋芯夾層結構。因此結合3D打印等新工藝技術及樹脂基復合材料輕質(zhì)高強的特點,為新型超材料聲襯的研發(fā)應用帶來了可能。


四、樹脂基復合材料在民用渦扇發(fā)動機應用的啟示
4.1 先進結構設計是航空發(fā)動機樹脂基復合材料應用的先導
復合材料各向異性的特點不僅給航空發(fā)動機復合材料部件設計帶來豐富選擇也帶來了巨大的挑戰(zhàn)。以復合材料風扇葉片為例,在設計過程中需考慮氣動性能以及服役過程中高轉速下異物沖擊、結構疲勞等問題。因而基于復合材料結構力學、空氣動力學、失效分析等多學科交叉融合,形成制件內(nèi)部細觀結構控制,整體外形尺寸精度把握、協(xié)調(diào)結構與氣動性能的多角度綜合設計理念尤為重要。3D打印新工藝和超材料新結構的出現(xiàn),給航空發(fā)動機復合材料構件設計提供了新的方向。應充分發(fā)揮新工藝、新結構的特點,拓展設計理念,優(yōu)化復雜構件設計思路。此外,在制件結構設計時,也應注意遴選材料體系的技術成熟度及制件成型工藝的可達性、高效性。實現(xiàn)“設計-材料-制造”一體化統(tǒng)籌規(guī)劃,發(fā)揮結構設計的先導作用。
4.2 高性能原材料是航空發(fā)動機樹脂基復合材料應用的基礎
先進增強材料及樹脂體系的不斷進步是推動樹脂基復合材料在航空發(fā)動機應用的重要基礎。從增強纖維來看,航空發(fā)動機部件用增強纖維經(jīng)歷了由傳統(tǒng)玻璃纖維到高性能碳纖維、芳綸纖維的轉變。從樹脂體系看,對環(huán)氧樹脂、雙馬樹脂和聚酰亞胺樹脂等高性能化的要求也日益提高?,F(xiàn)階段樹脂基復合材料在航空發(fā)動機風扇葉片等高速旋轉部件及內(nèi)部偏高溫部位的應用趨勢促使發(fā)動機用樹脂體系向高韌性化和高耐溫性方向發(fā)展。在挖掘纖維、樹脂本體性能潛力的同時,研發(fā)以微納材料為代表的第三相功能性組分,實現(xiàn)復合材料力學性能強化與功能特性拓展的平衡統(tǒng)一。從3D打印技術看,適用于不同3D打印工藝的成熟材料體系較少。因此實現(xiàn)3D打印材料體系的規(guī)范化、標準化開發(fā)驗證,保證原材料性能水平先進性和成熟性對3D打印航空發(fā)動機樹脂基復合材料部件發(fā)展應用具有重要意義。
4.3 高效低成本制造是航空發(fā)動機樹脂基復合材料應用的關鍵
高效低成本制造技術是保證航空發(fā)動機用復合材料構件穩(wěn)定批量化應用的關鍵。例如復合材料風扇葉片尺寸和形狀的精確性對發(fā)動機進氣效率、葉片運轉氣動穩(wěn)定性都具有至關重要的影響。目前復合材料葉片生產(chǎn)所采用的預浸料自動裁剪、激光定位鋪覆技術、纖維預成型體3D編織技術不僅保證了葉片尺寸的準確性,而且大大減少了后續(xù)修邊等工序,節(jié)省了人力、物力的支出。機械自動化已成為樹脂基復合材料成型工藝發(fā)展水平的重要標志。因此,需依據(jù)航空發(fā)動機用樹脂基復合材料制件精確化、高效化生產(chǎn)的要求,融合材料、機械、控制等不同學科,積極開展自動化設備的研制和應用工作,實現(xiàn)多方向交叉,不同專業(yè)促進共贏,推動樹脂基復合材料自動化制造。此外,針對小批量復雜結構件,采用3D打印技術無需模具工裝制造,可減少原材料浪費,避免模具工裝制造、原材儲備等環(huán)節(jié)大量資金投入。因而有利于降低航空發(fā)動機部件高昂的制造成本。
4.4 高可靠驗證評價是航空發(fā)動機樹脂基復合材料應用的保障
航空發(fā)動機用樹脂基復合材料制件服役過程中會經(jīng)受濕熱老化、疲勞振顫、異物沖擊等苛刻的工作條件。國外航空發(fā)動機復合材料風扇葉片經(jīng)歷了疲勞測試、除冰系統(tǒng)測試、喘振和旋轉失速裕度測試、吞鳥測試等實驗認證。復合材料機匣包容效果評測也需通過平板打靶、全尺寸包容性實驗等實驗考核。需要指出的是,復合材料制件在成型質(zhì)量評價和失效模式分析方面與傳統(tǒng)金屬材料存在不同,不能完全照搬原有金屬材料制件的評價標準。需通過材料級、元件級、制件級實驗數(shù)據(jù)積累及實際服役工況狀態(tài)采集,建立健全航空發(fā)動機用樹脂基合材料驗證數(shù)據(jù)庫和相應評價機制,推動樹脂基復合材料在航空發(fā)動機的應用。
經(jīng)過數(shù)10年的發(fā)展,樹脂基復合材料在民用渦扇發(fā)動機上得到了廣泛的應用。樹脂基復合材料不僅降低了航空發(fā)動機結構質(zhì)量,在發(fā)動機可靠性、經(jīng)濟性和環(huán)保性方面也起到了積極的推動作用。其用量已成為衡量航空發(fā)動機先進性的重要標志。國外在航空發(fā)動機復合材料應用方面已經(jīng)積累了大量實驗數(shù)據(jù)和服役經(jīng)驗,在多型航空發(fā)動機上已獲得較為成熟的應用。相比而言,我國在民用航空發(fā)動機樹脂基復合材料部件研發(fā)應用方面還存在一定差距。需要從結構設計、原材料、制造工藝、驗證評價等諸多方面進行趕超。相信隨著國內(nèi)樹脂基復合材料技術的日益進步,我國樹脂基復合材料在民用渦扇發(fā)動機的應用必將迎來突破性發(fā)展。