碳纖維復(fù)合材料(CFRP)由于具有高強(qiáng)度、高模量、低密度、耐高溫、耐腐蝕、耐摩擦、抗疲勞等優(yōu)異的性能,廣泛應(yīng)用于航空航天、國防軍事、汽車飛機(jī)構(gòu)件等領(lǐng)域。以空客A380為例,碳纖維復(fù)合材料的用量已經(jīng)達(dá)到32t左右,占機(jī)構(gòu)總量的15%,再加上其他種類的復(fù)合材料,估計其總用量可達(dá)結(jié)構(gòu)總重的25%左右。鉆削加工是碳纖維復(fù)合材料最常見的二次加工方式之一,制孔主要用于鉚接或者緊固結(jié)構(gòu)件。然而,碳纖維復(fù)合材料因其具有各向異性和非均勻性、層間結(jié)合強(qiáng)度低、受溫度影響大等特點(diǎn),在鉆削制孔過程中極易產(chǎn)生分層、毛刺和撕裂等缺陷,屬于典型的難加工材料。
研究表明,在上述幾種碳纖維復(fù)合材料常見的制孔缺陷中,分層缺陷對復(fù)合材料結(jié)構(gòu)件的承載能力和疲勞強(qiáng)度影響最大。本文主要從碳纖維復(fù)合材料鉆削加工過程中分層缺陷的產(chǎn)生機(jī)理、影響因素和檢測等方面對國內(nèi)外目前的研究現(xiàn)狀進(jìn)行綜述。CFRP的機(jī)理分析
由于CFRP力學(xué)性能的特殊性和內(nèi)部結(jié)構(gòu)的多樣性,在切削過程中,材料的變形過程遠(yuǎn)比金屬材料復(fù)雜得多,這不僅與刀具形狀及工藝參數(shù)等傳統(tǒng)因素有關(guān),還受纖維和基體屬性以及纖維鋪層方向的直接影響。因此,CFRP的切削加工機(jī)理與傳統(tǒng)的金屬切削加工機(jī)理有很大區(qū)別。1.CFRP的切削機(jī)理
在1983年,Koplev等較早對碳纖維切削過程進(jìn)行試驗(yàn)研究,指出CFRP切屑主要是由材料的脆性斷裂形成的。D.H.Wang等對單向和多向碳纖維復(fù)合材料進(jìn)行正交切削試驗(yàn),研究了不同的纖維方向?qū)η行夹纬蓹C(jī)制的影響。由于碳纖維復(fù)合材料由脆性的碳纖維和韌性的樹脂基體組成,兩者強(qiáng)度極限相差很大,前者是后者的若干倍,因此學(xué)者張厚江等認(rèn)為在切削過程中可以將其簡化地看成只是對碳纖維的切削,而將對樹脂基體的切削忽略。
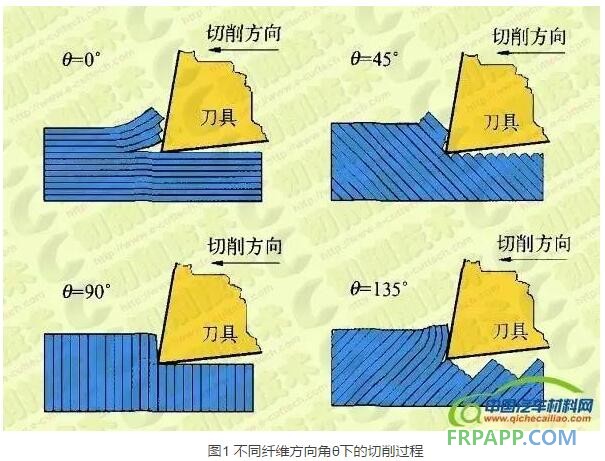
文獻(xiàn)對一些典型的纖維鋪層方向進(jìn)行研究,總結(jié)碳纖維復(fù)合材料在不同的纖維方向角θ下切屑的形成形式(見圖1)。當(dāng)θ=0°時,切屑的形成是刀具通過不斷地將切削層材料與基體材料分離開而實(shí)現(xiàn)的。這種切削變形形式稱為層間分離型。
當(dāng)0°<θ≤90°時,以圖1中θ=45°和θ=90°為代表,刀具切削刃對碳纖維復(fù)合材料的推擠作用在纖維內(nèi)部形成垂直于纖維自身軸線的剪切應(yīng)力。當(dāng)剪切應(yīng)力超過纖維剪切強(qiáng)度極限時,纖維被切斷。切斷后的纖維在刀具前刀面的推擠作用下,沿纖維方向產(chǎn)生滑移。當(dāng)滑移引起的纖維界面間的剪切應(yīng)力超過基體樹脂材料的剪切強(qiáng)度極限時,被切斷纖維與其他纖維分離,形成切屑。這種切削變形形式稱為纖維切斷型。當(dāng)90°<θ<180°時,以圖1中θ=45°為代表,刀具對前端材料的推擠作用導(dǎo)致復(fù)合材料間的層間分離。刀具前端材料在刀具作用下發(fā)生彎曲,當(dāng)彎曲應(yīng)力超過碳纖維復(fù)合材料的彎曲強(qiáng)度極限時,底部發(fā)生斷裂。刀具繼續(xù)前進(jìn),刀具對其前端材料推擠作用加強(qiáng),當(dāng)前端材料底部斷裂點(diǎn)處的剪切應(yīng)力超過材料剪切強(qiáng)度極限時,發(fā)生剪切斷裂,形成切屑。這種切削變形形式稱為彎曲剪切型。
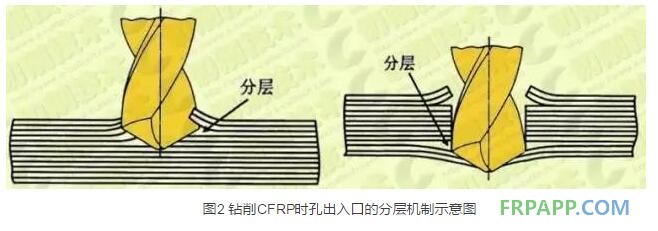
2.分層產(chǎn)生機(jī)理分析分層是指由層間應(yīng)力或制造缺陷等引起的復(fù)合材料鋪層之間的脫膠分離破壞現(xiàn)象。研究表明,鉆削碳纖維復(fù)合材料過程中的分層缺陷可以分為兩種損傷機(jī)制:入口剝離分層和出口頂出分層(見圖2)。在鉆削過程中,一方面,當(dāng)鉆頭橫刃開始接觸材料而主切削刃未完全切入材料時,切削力會將被切除的材料推入螺旋槽。這些材料在切斷之前會沿著螺旋槽表面上升,產(chǎn)生向上的剝離力。剝離力會使上層未切除的區(qū)域產(chǎn)生分離,即為剝離分層。另一方面,當(dāng)鉆頭的橫刃即將鉆出材料時,由于材料剩余的未切除的材料層數(shù)越來越少,在軸向力超過材料的層間結(jié)合強(qiáng)度時,出口周邊的鋪層之間發(fā)生脫粘現(xiàn)象而造成頂出分層缺陷。頂出分層發(fā)生在層間區(qū)域,因此它不僅取決于纖維的性質(zhì),而且和樹脂的性質(zhì)有關(guān)。對于分層的產(chǎn)生機(jī)理,張厚江等通過聲學(xué)顯微鏡分析指出,CFRP板材鉆削孔入口側(cè)和出口側(cè)都有分層,入口側(cè)分層為圓形,出口側(cè)表層分層為橢圓形,深層分層為圓環(huán)型;同一孔出口側(cè)的分層遠(yuǎn)遠(yuǎn)大于入口側(cè)的分層。
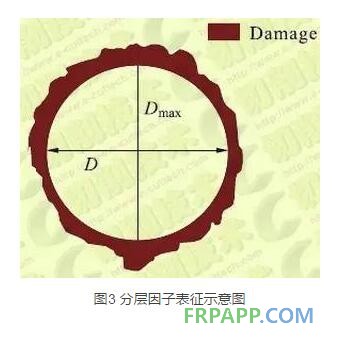
分層的影響因素影響鉆削分層缺陷的因素有很多,包括切削參數(shù)、刀具、材料性質(zhì)、制造工藝等。這些影響因素之間存在相互耦合的關(guān)系,而且在鉆削過程中還受到很多不可控因素的影響。目前,國內(nèi)外學(xué)者研究較多的是切削參數(shù)與刀具對分層缺陷的影響。研究表明,鉆削過程中的軸向力是導(dǎo)致分層缺陷的最主要原因。在鉆削加工過程中,當(dāng)軸向力超過一個閥值時,分層缺陷就會發(fā)生。其中,橫刃對軸向力的貢獻(xiàn)約占60%左右。
1.切削參數(shù)影響切削參數(shù)變量主要包括切削速度、進(jìn)給量f(每齒進(jìn)給量fz)等因素。切削速度和進(jìn)給量是鉆削加工過程中的兩個主要參數(shù)變量。研究表明,進(jìn)給量對分層缺陷的影響大于切削速度。António T.Marques等采用4種不同的鉆頭研究了其在不同切削參數(shù)下的切削加工性能。試驗(yàn)表明,合理選擇切削參數(shù)可以減小軸向力,進(jìn)而減小分層缺陷影響。試驗(yàn)研究指出以0.025mm/r的進(jìn)給速度和53m/min的切削速度切削材料可以使軸向力和分層因子達(dá)到最小,分層因子下降大概4%-5%左右。V.N.Gaitonde等用硬質(zhì)合金鉆頭(K20)對碳纖維復(fù)合材料進(jìn)行鉆削加工試驗(yàn)研究,結(jié)果表明分層趨勢隨著切削速度的增加而減小,并且采用低進(jìn)給量和頂角可以減小分層因子。張厚江等采用YG6X整體硬質(zhì)合金四面鉆頭鉆削CFRP時,發(fā)現(xiàn)進(jìn)給量對各層間分層的影響呈上凹曲線。在進(jìn)給量很小時,進(jìn)給量增大分層尺寸降低;當(dāng)進(jìn)給量超過時,進(jìn)給量增大,各層間分層尺寸上升。因此是產(chǎn)生最小分層的進(jìn)給量,是一個臨界值。
Vijayan Krishnaraj等采用K20硬質(zhì)合金鉆頭在不同主軸轉(zhuǎn)速和進(jìn)給量的情況下研究碳纖維復(fù)合材料的切削加工性能。試驗(yàn)表明,入口側(cè)剝離分層因子與進(jìn)給速率之間并沒有明顯的規(guī)律,但是從總體上看,低進(jìn)給速率的分層因子小于高進(jìn)給速率的分層因子。出口側(cè)頂出分層因子隨著進(jìn)給速率和主軸速率的增加而增大。進(jìn)給速率是出口側(cè)頂出分層因子的主要影響因素。進(jìn)給速率的貢獻(xiàn)率是51.4%,而主軸轉(zhuǎn)速的貢獻(xiàn)率是35.42%。試驗(yàn)還給出了最優(yōu)的進(jìn)給速率和主軸轉(zhuǎn)速,分別為0.137mm/r和12000r/min。
2.刀具的影響由于碳纖維復(fù)合材料屬于典型的難加工材料,并且鉆孔加工屬于半封閉加工,切削加工過程中產(chǎn)生的大量熱不易被切屑和刀具帶走。因此,鉆削加工容易導(dǎo)致刀具的磨損。刀具的磨損不僅影響制孔質(zhì)量而且也會影響制孔效率和增加加工成本。刀具的影響因素主要包括刀具幾何形狀、刀具涂層、刀具參數(shù)等。由于導(dǎo)致分層缺陷的臨界軸向力受切削刃的影響,因此刀具幾何結(jié)構(gòu)對于減小分層缺陷有著重要的作用。Luís Miguel P.Dur?o等研究了五種刀具:120°頂角麻花鉆、85°頂角麻花鉆、鋸齒鉆、匕首鉆、階梯鉆。研究表明,120°頂角麻花鉆的分層因子最小,階梯鉆的分層因子次之,且與120°頂角麻花鉆的分層因子相差不大。分層因子最大的為鋸齒鉆,達(dá)到了1.23左右。因此,根據(jù)該試驗(yàn)條件最佳的刀具為120°頂角麻花鉆,階梯鉆次之。對于硬質(zhì)合金涂層刀具,目前常用的主要有普通涂層(如AlTiN)和金剛石涂層等類型。Xin Wang等對比試驗(yàn)研究了三種不同的刀具:未涂層硬質(zhì)合金鉆頭、金剛石涂層硬質(zhì)合金鉆頭和AlTiN涂層硬質(zhì)合金鉆頭。試驗(yàn)結(jié)果表明,金剛石涂層可以顯著減少刀具的磨損,然而AlTiN涂層硬質(zhì)合金鉆頭由于在鉆削過程中出現(xiàn)氧化現(xiàn)象而未能有效降低刀具磨損速率。Redouane Zitoune等用納米涂層硬質(zhì)合金鉆頭對碳纖維和鋁合金疊層材料進(jìn)行鉆削加工。他們指出,在鉆削CFRP過程中,采用納米涂層硬質(zhì)合金鉆頭可以顯著降低粗糙度和軸向力。軸向力的降低可以有效預(yù)防鉆削過程中的分層缺陷。
3.其他影響因素影響分層缺陷的因素很多,除了上述廣泛研究的切削參數(shù)和刀具外還有其他重要的影響因素,比如材料的預(yù)浸漬方式、導(dǎo)孔的影響、墊板的影響、新工藝等。Islam Shyha等對比分析了3種類型預(yù)浸漬材料(977-2/HTS AC、8552/AS4 AC、MTM44-1/HTS OC)對鉆削過程的影響。研究表明在入口側(cè)分層缺陷,預(yù)浸漬方式的貢獻(xiàn)率為12%;然而,在出口側(cè)分層缺陷,預(yù)浸漬方式的貢獻(xiàn)率已經(jīng)高達(dá)38.5%。另外,8552/AS4 AC預(yù)浸材料的分層因子較大,特別是在高進(jìn)給速度(0.4mm/r)的情況下,該現(xiàn)象更為明顯。C.C.Tsao和H.Hocheng研究了導(dǎo)孔對分層缺陷的影響,其中導(dǎo)孔的直徑與套料鉆的內(nèi)徑相等。試驗(yàn)結(jié)果表明,雖然分層臨界軸向力由于導(dǎo)孔而降低,但是鉆削過程中的軸向力也由于切屑的去除而大大降低??刂祁A(yù)制導(dǎo)孔直徑與鉆孔直徑的比值,可以在較大進(jìn)給量情況下鉆削加工碳纖維復(fù)合材料而不出現(xiàn)分層缺陷。C.C.Tsao和H.Hocheng通過在被加工材料底部安裝墊板,研究其對分層缺陷的影響。他們首先推導(dǎo)出鋸齒鉆和套料鉆帶墊板鉆削的分層臨界軸向力模型公式,隨后進(jìn)行了試驗(yàn)驗(yàn)證。研究表明,安裝墊板可以較未安裝墊板獲得更好的鉆孔質(zhì)量。近年來,科研人員在對鉆削制孔機(jī)理進(jìn)行大量的研究基礎(chǔ)上,試驗(yàn)了一些新的制孔方法和材料處理工藝,并取得了一定的成果。本文以螺旋銑削制孔技術(shù)和縫合技術(shù)為例。螺旋銑削制孔技術(shù)是利用銑削原理進(jìn)行制孔的新型切削加工方法。在螺旋銑削過程中,通過改變刀具與孔軸線之問的偏心距而得到不同的孔徑,因此可以實(shí)現(xiàn)同一刀具針對不同孔徑的制孔及锪窩加工,從而降低了加工成本,提高了加工效率。王奔等以傳統(tǒng)鉆削加工為參照,分別利用螺旋銑削及傳統(tǒng)鉆削兩種方法對C/E復(fù)合材料進(jìn)行制孔試驗(yàn),并對螺旋銑削與傳統(tǒng)鉆削刀具的運(yùn)動軌跡進(jìn)行分析。結(jié)果表明,切削溫度是影響C/E復(fù)合材料制孔質(zhì)量的重要因素。因?yàn)?,螺旋銑削制孔時的切削溫度較傳統(tǒng)鉆削時降低69℃以上,降幅大于36%,因此有效避免了制孔出口處的撕裂及分層現(xiàn)象。縫合技術(shù)作為一種復(fù)合材料液體成型預(yù)制體的有效連接增強(qiáng)的方法,其原理是通過縫合手段,使復(fù)合材料在垂直于鋪層平面的方向得到增強(qiáng),從而提高材料層間損傷容限。穿過增強(qiáng)織物厚度方向的縫線可以大大改善復(fù)合材料的層間性能。Yosra Turki等試驗(yàn)研究了縫合與未縫合復(fù)合材料的鉆削加工性能。結(jié)果表明,縫合材料在表面質(zhì)量和缺陷減少方面比未縫合材料有很大的改進(jìn)??p合線使層間產(chǎn)生壓縮效應(yīng)并且在鉆頭的推進(jìn)過程中,阻礙其分離。因此,縫合技術(shù)可以減少由軸向力導(dǎo)致的分層缺陷和基質(zhì)破裂。K.T.Tan等還研究了縫合密度和縫合線厚度對碳纖維復(fù)合材料的破壞形式和失效特性的影響。
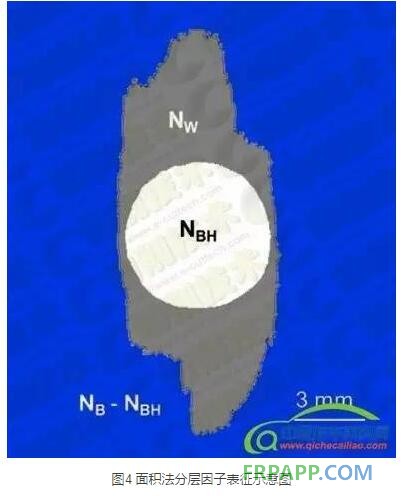
分層缺陷的檢測為了檢測分層缺陷的程度,國內(nèi)外科研人員研究試驗(yàn)了許多種方法。張厚江等采用氯化金滲透液檢測法較早對碳纖維復(fù)合材料鉆削制孔分層缺陷進(jìn)行檢測。檢測試驗(yàn)中發(fā)現(xiàn),分層缺陷的形狀主要有近似橢圓形和近似圓形兩種,兩者的中心都與孔中心重合。隨后,他們又采用聲學(xué)顯微鏡對碳纖維復(fù)合材料鉆孔分層缺陷進(jìn)行檢測,根據(jù)檢測試驗(yàn)結(jié)果及分析,總結(jié)出了立體分層模型,并對分層形成機(jī)理進(jìn)行了探討。為避免對材料產(chǎn)生人為損傷,無損檢測技術(shù)在分層缺陷檢測方面得到了廣泛運(yùn)用。目前采用的無損檢測技術(shù)主要包括聲學(xué)顯微鏡、超聲C掃描、X射線電腦斷層攝影技術(shù)、增強(qiáng)射線照相法等。周正干等基于激光超聲技術(shù),對復(fù)合材料緊固孔分層進(jìn)行量化表征試驗(yàn);基于穿透法和脈沖反射法進(jìn)行激光超聲C掃描檢測,得到緊固孔區(qū)域分層缺陷的形狀、尺寸和位置特征。研究結(jié)果表明,利用激光超聲技術(shù)的非接觸式激發(fā)、接收和高分辨力特點(diǎn),可以準(zhǔn)確測得緊固孔區(qū)域分層缺陷導(dǎo)致的波反射和衰減,有效表征飛機(jī)復(fù)合材料結(jié)構(gòu)的緊固孔分層缺陷。
C.C.Tsao和H.Hocheng采用X射線電腦斷層攝影技術(shù)和超聲C掃描技術(shù)這兩種無損檢測技術(shù)對分層缺陷進(jìn)行檢測。試驗(yàn)結(jié)果表明X射線電腦斷層攝影技術(shù)和超聲C掃描技術(shù)測得的結(jié)果很接近,這兩項(xiàng)技術(shù)都可以揭示不同刀具分層發(fā)生的臨界軸向力。然而X射線電腦斷層攝影技術(shù)對于檢測分層缺陷更加靈活和有效。結(jié)語隨著對碳纖維復(fù)合材料性能要求越來越高、工作條件越來越苛刻,對碳纖維復(fù)合材料制孔質(zhì)量要求也越來越高。分層作為鉆削制孔過程中的主要缺陷之一,國內(nèi)外學(xué)者已經(jīng)對其產(chǎn)生機(jī)理和影響因素進(jìn)行了深入研究。通過優(yōu)化合理選擇切削參數(shù)和采用不同幾何形狀和涂層的刀具是目前減少分層缺陷的有效途徑。通過對國內(nèi)外對碳纖維復(fù)合材料分層缺陷的研究現(xiàn)狀進(jìn)行綜述,今后可從以下方面加大對碳纖維復(fù)合材料制孔分層缺陷的研究:繼續(xù)研究新的刀具及優(yōu)化刀具幾何結(jié)構(gòu)參數(shù)以提高其切削性能;對復(fù)合材料進(jìn)行深入研究,改善制造工藝,提高材料性能;建立完善、合理的仿真模型,以期達(dá)到對分層缺陷更準(zhǔn)確的預(yù)測。