日本東麗3月28日宣布推出新的碳纖維復(fù)合材料成型工藝,不僅可以提高部件的尺寸精度,還能降低生產(chǎn)過(guò)程的能耗。該技術(shù)在經(jīng)過(guò)實(shí)證之后,將首先應(yīng)用于飛機(jī)制造,然后向汽車和其他一般產(chǎn)業(yè)進(jìn)行推廣。
傳統(tǒng)的CFRP部件通常采用熱壓罐工藝生產(chǎn)。首先將預(yù)浸料鋪設(shè)在模具中,然后送入熱壓罐進(jìn)行加熱、固化、成型。但由于以空氣作為介質(zhì)導(dǎo)熱很慢,而且如果模具本身比熱容較大、吸收了大量的熱量,會(huì)導(dǎo)致部件本身升溫的時(shí)間很長(zhǎng),成型速度很慢。這一直是令業(yè)內(nèi)專家頭疼的難題。
再者,一旦所需成型的部件尺寸較大、厚度可觀,或者幾何形狀較為復(fù)雜,部件內(nèi)部就會(huì)產(chǎn)生殘留應(yīng)力分布不均的問(wèn)題,導(dǎo)致成型后的部件容易變形。譬如在飛機(jī)機(jī)翼的組裝過(guò)程中,為了避免這種情況,必須加入一些填料,付出額外的人力、物力和時(shí)間。這些額外的工序會(huì)進(jìn)一步拉長(zhǎng)整個(gè)生產(chǎn)周期。
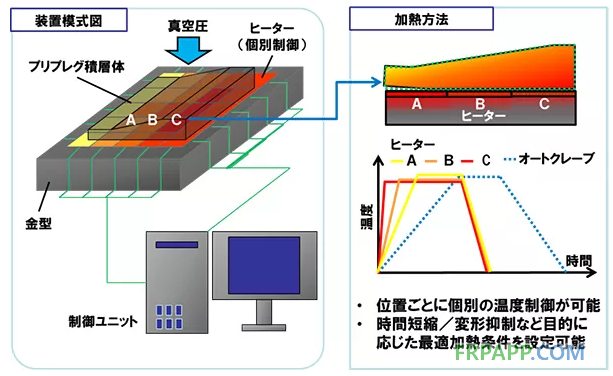
為解決上述問(wèn)題,日本東麗在模具表面安裝了既定數(shù)量的加熱器,(將模具表面分割成若干加熱區(qū)),在真空條件下進(jìn)行接觸加熱。這種方法不僅提高了加熱效率,同時(shí)降低了能量消耗。更令人稱道的是,每個(gè)加熱器(加熱區(qū))都是獨(dú)立控制的,針對(duì)部件的不同位置施以最合適的溫度。這樣做可以使部件內(nèi)部的殘留應(yīng)力實(shí)現(xiàn)均勻分布,部件可以最大程度接近預(yù)先設(shè)計(jì)的尺寸和形狀,解決了之前存在的一系列問(wèn)題,減少了組裝過(guò)程所需的人力、物力和時(shí)間。
為了實(shí)現(xiàn)對(duì)不同加熱區(qū)進(jìn)行精準(zhǔn)溫控的目標(biāo),日本東麗與愛媛大學(xué)、東京理工大學(xué)共同開發(fā)了能夠預(yù)測(cè)部件形變并對(duì)加熱溫度進(jìn)行相應(yīng)調(diào)整的模擬軟件,將部件成型的時(shí)間壓縮到最短,將尺寸的誤差下降到最低。目前該項(xiàng)目的試制裝置已經(jīng)到位,實(shí)驗(yàn)論證工作正在有序推進(jìn)中。
若是依照傳統(tǒng)的熱壓罐成型工藝,要生產(chǎn)大尺寸的CFRP飛機(jī)部件,需要耗費(fèi)9個(gè)小時(shí)的時(shí)間。但若是依照此次東麗開發(fā)的新成型工藝,則可以將生產(chǎn)周期縮短到4個(gè)小時(shí)。另外,新的工藝可以節(jié)省50%的能耗(因?yàn)椴扇≈苯咏佑|加熱的方式,免除了加熱/加壓的媒介),還可以提高尺寸精度,減少填料的用量,縮短組裝耗費(fèi)的工時(shí)。