提示:本文中出鏡的中國國際復(fù)材展展商有迪芬巴赫、恩格爾。

TxV公司生產(chǎn)的飛機(jī)行李艙B支架具備高強(qiáng)度和復(fù)雜的幾何外觀,這都?xì)w因于采用了混合材料復(fù)合模塑工藝技術(shù)。
通常,航空航天企業(yè)愿意為獲得更加適合的復(fù)合材料零部件付出更多成本,因為他們知道這樣的付出必有回報。因為質(zhì)量輕,它能減少油耗;因為耐用,它的服役壽命更長,還能減少運維成本。這種從“全生命周期”考慮問題的視角為復(fù)合材料打開了很多終端應(yīng)用市場的大門。然而,即便具備上述種種優(yōu)勢,它在成本上的劣勢也是顯而易見的。眾所周知,現(xiàn)有條件下,復(fù)合材料零部件的生產(chǎn)成本遠(yuǎn)高于金屬材料。
然而,這種局面正在悄然發(fā)生變化。
由美國TxV Aero Composites公司推出的新的復(fù)合材料自動化生產(chǎn)技術(shù)正在將低成本的天平向復(fù)合材料一方傾斜,這種技術(shù)被稱之為“混合材料復(fù)合模塑工藝”。
TxV Aero Composites公司是由美國Tri-Mack Plastics Manufacturing公司和英國威格斯公司(Victrex)共同成立的合資企業(yè),其所推出的“混合材料復(fù)合模塑工藝”自問世起,目標(biāo)就直指商業(yè)化規(guī)模量產(chǎn)。目前,TxV公司已與德國SFS intec Aircraft Components公司合作(以下簡稱SFS intec),放棄了此前一直采用的航空鋁料,經(jīng)過重新設(shè)計,轉(zhuǎn)而推出了復(fù)合材料飛機(jī)行李艙支架產(chǎn)品,并具備了量產(chǎn)能力。該產(chǎn)品的成功面世,顯示出“混合材料復(fù)合模塑工藝”以及威格斯旗下品牌名為VICTREX AE 250的碳纖維/PAEK單向預(yù)浸帶產(chǎn)品在眾多航空領(lǐng)域的應(yīng)用潛力。如果把傳統(tǒng)金屬部件的生產(chǎn)稱之為一種“減材工藝”,那么復(fù)合材料部件的生產(chǎn)則可稱之為一種“增材工藝”。
從“減材”到“增材”
機(jī)械師經(jīng)常戲稱自己是“廢料制造機(jī)”,因為在將金屬板材加工成為金屬部件的過程中,會產(chǎn)生大量的碎片和廢料。它們或被回收、或被處理、或被旋即重新投入生產(chǎn)。但不管采用哪種方式,都改變不了浪費的事實,還直接拉高了生產(chǎn)成本。據(jù)稱,以SFS intec公司生產(chǎn)的飛機(jī)行李艙鋁支架為例,在經(jīng)過一系列機(jī)加工環(huán)節(jié)之后,廢料的發(fā)生比率高達(dá)60%-70%。
正因為有著如此之高的廢料發(fā)生率,僅從原材料角度考慮,不管是生產(chǎn)凈成型還是近凈成型支架,復(fù)合材料的成本都比鋁低。“盡管鋁料便宜,但因為廢料發(fā)生率高,給了復(fù)合材料從成本角度一較高下的機(jī)會。特別是當(dāng)BTF比率(購買-飛行比率)達(dá)到8:1(廢料發(fā)生率高達(dá)87.5%)的時候,大多數(shù)買來的鋁都浪費了。”TxV公司高級客戶經(jīng)理Jonathan Sourkes表示,“另外,從生產(chǎn)周期角度考慮,復(fù)合材料也極具優(yōu)勢,它能夠?qū)⑸a(chǎn)周期從數(shù)小時縮短到數(shù)分鐘。”
除此之外,復(fù)合材料還能賦予零部件復(fù)雜的幾何外觀,從而滿足特定的載荷能力。這對于傳統(tǒng)工藝而言,是無法在低成本條件下實現(xiàn)的目標(biāo)。設(shè)想,如果以短切纖維為原料,輔之以注塑這類速度快、人工介入少的工藝,生產(chǎn)出的零部件成本較低,但無法獲得足夠的載荷能力;與之相反,如果以連續(xù)纖維為原料,輔之以速度慢、人工介入頻繁的工藝,生產(chǎn)出的零部件能夠獲得足夠的載荷能力,但造價卻十分昂貴。
基于以上矛盾的存在,復(fù)合材料行業(yè)投入了巨大的資源,意圖開發(fā)出一種兼具高效率、低成本,同時又能賦予零部件較高載荷能力的自動化生產(chǎn)工藝,以滿足航空航天領(lǐng)域客戶的特定需求。在此背景下,經(jīng)過威格斯公司和Tri-Mack公司協(xié)商,以推動PAEK基復(fù)合材料的航空應(yīng)用為己任,于2017年正式成立TxV公司。
虛擬原型設(shè)計:無需實際生產(chǎn)出樣件,TxV公司就可以對鋪放和片層取向進(jìn)行反復(fù)驗證,直到載荷能力達(dá)到設(shè)計要求。
步驟二:坯料進(jìn)入自動模壓單元,用一熱一冷兩套壓板將其壓實、冷卻。
步驟三:B支架初始形態(tài)完成
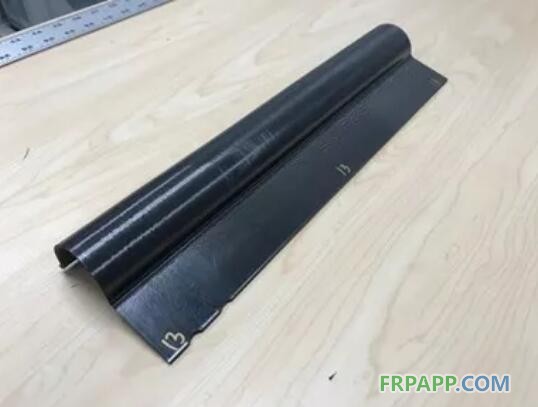
步驟四:用水刀切割坯料,切出碳纖維/PAEK嵌入件。每個支架上需要2個這樣的嵌入件。
第五步,利用恩格爾公司(ENGEL)提供的高溫注塑機(jī)進(jìn)行復(fù)合模塑。將嵌入件置于注塑機(jī)腔體內(nèi),并注入熔化的PEEK。由于嵌入件采用PAEK LM制造,熔點較低,表面部分會與熔融的PEEK緊密結(jié)合在一起。
步驟五:利用恩格爾高溫注塑機(jī)機(jī)進(jìn)行復(fù)合模塑成型
第六步,如果需要,還可對注塑成形的部件進(jìn)行機(jī)加工直至凈成型。“雖然我們的目標(biāo)是達(dá)到近凈成型,”Soukers解釋說,“但多數(shù)情況下,為了確保產(chǎn)品的實際幾何外觀與設(shè)計準(zhǔn)確無二,還需要進(jìn)行最小程度的機(jī)加工。”這部分操作通常利用水刀或者在CNC數(shù)控加工中心完成。
步驟六:B支架最終成型,生產(chǎn)周期約為3分鐘,BTF數(shù)值達(dá)到1.06:1,減重30%-40%。

由TxV公司推出的混合材料復(fù)合模塑工藝具備兩個關(guān)鍵優(yōu)勢。其一,對部件中連續(xù)纖維增強(qiáng)部分實現(xiàn)了自動化生產(chǎn);其二,充分利用注塑工藝生產(chǎn)效率高的特性并實現(xiàn)了復(fù)雜的幾何外形。需要強(qiáng)調(diào)的是,在實現(xiàn)上述目標(biāo)的過程中,TxV先是生產(chǎn)出滿足載荷要求的片層(Laminates),再將其進(jìn)行復(fù)合模塑成型,實現(xiàn)其功能化,并賦予其最終的幾何外觀。SFS intec公司創(chuàng)新事業(yè)部主任Sascha Costabel表示說:“傳統(tǒng)工藝中,零部件的高載荷能力和復(fù)雜幾何外觀需要通過一系列操作才能實現(xiàn)。與之相比,TxV所推出的新工藝真是一個不錯的選擇。”
Sourkes表示,TxV公司將SFS視為絕佳的合作伙伴:“作為系統(tǒng)附件產(chǎn)品的全球領(lǐng)導(dǎo)者,SFS公司對新技術(shù)保有一貫的濃厚興趣。他們具備創(chuàng)新的精神,具有投資新技術(shù)的強(qiáng)烈意愿。” 另外,SFS intec公司還和航空界客戶保持著緊密的聯(lián)系,同時具備認(rèn)證資質(zhì)。這對于經(jīng)過重新設(shè)計的航空零部件而言十分重要。
這款飛機(jī)行李艙支架也被稱為“B支架”,因其在設(shè)計和生產(chǎn)方面都極具挑戰(zhàn)性,所以被選為首個利用復(fù)合材料進(jìn)行重新設(shè)計的航空附件產(chǎn)品。借助Altair公司提供的有限元分析工具,經(jīng)過聯(lián)合工程設(shè)計、產(chǎn)品概念設(shè)計和模型設(shè)計,項目團(tuán)隊從第一個樣件開始就進(jìn)行了反復(fù)測試、驗證并最終證明了模型的成功。TxV公司表示,研發(fā)的關(guān)鍵在于堅持“設(shè)計服務(wù)于生產(chǎn)”的理念,在于充分利用了連續(xù)纖維自動鋪帶技術(shù)和短切纖維高速注塑技術(shù)的優(yōu)勢。
B支架的生產(chǎn)
在混合材料復(fù)合模塑工藝中,使用了相同級別、不同類型但特性突出的多種聚合物原材料。以B支架為例,與連續(xù)纖維增強(qiáng)部分配合使用的是PAEK,而在復(fù)合模塑外圍部分則采用了PEEK。PAEK和PEEK產(chǎn)品均由威格斯公司提供,具備卓越的抗疲勞性、耐化學(xué)腐蝕性,耐煙火毒性、快速成型性和出色的可焊接性。其中,VICTREX AE 250是一款低熔點PAEK材料(LM PAEK),熔點比PEEK低40攝氏度。“當(dāng)熔化的PEEK流經(jīng)LM PAEK復(fù)合材料表面時,二者會更好地熔結(jié)在一起。”
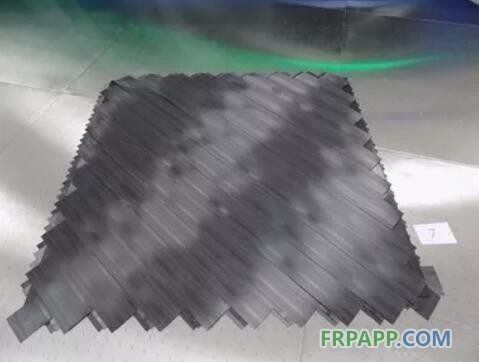
生產(chǎn)B支架時所采用的關(guān)鍵原材料包括:品牌名為VICTREX AE 250、寬度為2英寸的單向碳纖維/PAEK預(yù)浸帶(碳纖維含量58%)以及品牌名為VICTREX PEEK 150CA30的短切纖維PEEK模塑料(碳纖維含量30%)。這些原料在喂入混合材料復(fù)合模塑生產(chǎn)單元之后,歷經(jīng)下列步驟逐步成型:
第一步,利用迪芬巴赫提供的Fiberforge 2000鋪帶系統(tǒng),鋪放碳纖維/PAEK預(yù)浸帶。“這是目前世界上最快的鋪帶系統(tǒng)之一,”Sourkes表示。它可以與機(jī)器人配合使用,無間斷裝填并鋪放預(yù)浸帶。整個鋪放過程經(jīng)過了嚴(yán)密的設(shè)計,以確保預(yù)浸帶之間最小的孔隙率。同時,每鋪放一層之前,都會對上一層進(jìn)行重新檢測。上述流程在嚴(yán)密控制的環(huán)境下進(jìn)行,確保不受外界雜物和碎屑(FOD)的干擾。
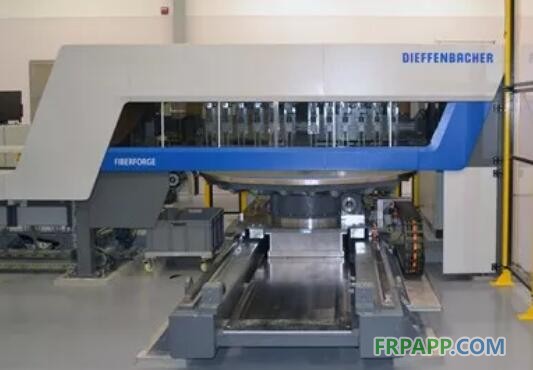
步驟1:利用迪芬巴赫Fiberforge 2000自動鋪帶機(jī)生產(chǎn)坯料。
第二步,在鋪放完成之后,坯料被送入自動模壓單元。先用一套加熱過的壓板壓實,去除內(nèi)部孔隙;再用一套冷壓板對坯料進(jìn)行冷卻。采取這樣“一冷一熱”兩套壓板的作業(yè)方式要比單純采用一套壓板效率更高。“直接的好處就是零部件的生產(chǎn)周期可以從數(shù)小時縮短到數(shù)分鐘。”Sourkes表示說。


第三步,壓實之后,形成預(yù)制件,并被送入下一個工作單元,完成支架的初始形態(tài)。
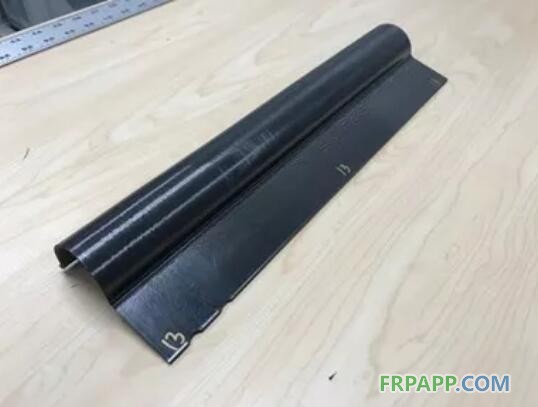
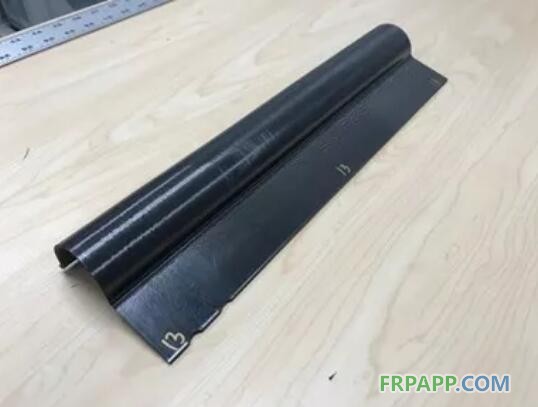

第四步,用Flow International公司提供的水刀對預(yù)制件進(jìn)行裁切,生產(chǎn)出碳纖維/PAEK嵌入件。
“每個項目都需要權(quán)衡預(yù)制件的尺寸。”Sourkes指出,”如果計算得當(dāng),一塊預(yù)制件上可以切出3-4個長方形嵌入件。這樣做能夠有效減少浪費,但會相應(yīng)延長水刀切割的作業(yè)時間。”以B支架為例,一塊預(yù)制件上能夠切出數(shù)塊小的嵌入件。

第五步,利用恩格爾公司(ENGEL)提供的高溫注塑機(jī)進(jìn)行復(fù)合模塑。將嵌入件置于注塑機(jī)腔體內(nèi),并注入熔化的PEEK。由于嵌入件采用PAEK LM制造,熔點較低,表面部分會與熔融的PEEK緊密結(jié)合在一起。

第六步,如果需要,還可對注塑成形的部件進(jìn)行機(jī)加工直至凈成型。“雖然我們的目標(biāo)是達(dá)到近凈成型,”Soukers解釋說,“但多數(shù)情況下,為了確保產(chǎn)品的實際幾何外觀與設(shè)計準(zhǔn)確無二,還需要進(jìn)行最小程度的機(jī)加工。”這部分操作通常利用水刀或者在CNC數(shù)控加工中心完成。

突破性進(jìn)展
在B支架的生產(chǎn)過程中,混合材料復(fù)合模塑工藝成功地將生產(chǎn)周期控制在3分鐘,將BTF數(shù)值控制在1.06:1(廢料發(fā)生率約為5.7%)。“借此技術(shù),原材料得到了最充分的利用,生產(chǎn)效率得到了提高,我們?yōu)榭蛻籼峁┝烁吒郊又档臒崴苄詮?fù)合材料零部件,還降低了金屬部件的設(shè)計成本。”生產(chǎn)結(jié)果顯示,B支架的重量下降了30%-40%,生產(chǎn)成本節(jié)約了20%-30%,其幾何外觀和各項參數(shù)性能均達(dá)到現(xiàn)有金屬部件水平。”如果給我們一個機(jī)會,對部件系統(tǒng)進(jìn)行完全重新設(shè)計,減重的比率最高能達(dá)到60%。”
此外,這款碳纖維/PAEK/PEEK行李艙支架還有效減少了部件的數(shù)量。此前,支架的配套底托采用PEEK材料制造,靠2個鉚釘固定在支架底部。如今,TxV和SFS雙方已商定利用同樣的復(fù)合模塑工藝,在支架底部直接復(fù)合成型一個底托。
毋庸置疑,混合材料復(fù)合模塑工藝的成功離不開TxV公司背后兩家股東的技術(shù)支持。Sourkes解釋說,完成PAEK材料和相關(guān)工藝的開發(fā)后,威格斯首先在現(xiàn)有合作伙伴中尋找合作機(jī)會。“然而,掌握注塑訣竅的公司往往不具備處理連續(xù)纖維的能力,而掌握連續(xù)纖維加工能力的公司又往往對注塑工藝知之甚少。”受此制約,在TxV公司和聚酮復(fù)合材料創(chuàng)新中心成立之前,威格斯和Tri-Mack公司對這兩個關(guān)鍵技術(shù)點已經(jīng)進(jìn)行了多年的合作研發(fā)。
在被要求對混合材料復(fù)合模塑工藝和傳統(tǒng)工藝進(jìn)行比較時,Soukes表示,傳統(tǒng)工藝無法對B支架進(jìn)行修復(fù),尤其從成本角度考慮是極不可行的。
首飛認(rèn)證
借助SFS intec公司具備認(rèn)證資質(zhì)這一優(yōu)勢,雙方已經(jīng)為這款B支架申請了單獨的適航認(rèn)證。“因為B支架需要懸空安裝在頭頂,在使用過程中很容易達(dá)到額定載荷。”Sourkes表示說,“尤其在起飛和降落階段,實際載荷會更大。”TxV公司和SFS公司希望這款部件能夠在2020年年初上機(jī)飛行。
一旦取得適航認(rèn)證,TxV將啟動B支架的量產(chǎn)工作。Sourkes強(qiáng)調(diào)說,TxV可以利用自有生產(chǎn)線進(jìn)行生產(chǎn),也愿意為感興趣的潛在合作伙伴提供技術(shù)支持,利用他們的生產(chǎn)線進(jìn)行生產(chǎn)。
這款B支架產(chǎn)品有望為同類復(fù)合材料產(chǎn)品打開更加廣闊的市場大門。根據(jù)預(yù)測,一架民航飛機(jī)上需要數(shù)以千計的支架及其他系統(tǒng)附件產(chǎn)品。一旦采用復(fù)合材料,這些產(chǎn)品將幫助飛機(jī)減少自重、降低成本。“毫無疑問,熱塑性復(fù)合材料零部件將在航空航天市場扮演越來越重要的角色。”Costable表示說。